CAE技術者にも、データ分析のスキルが求められる時代になりつつあります。
本稿では、データ分析がなぜCAE技術者に必要なのか、具体的な進め方と、よく突き当たる壁について紹介します。
データ分析とは
データ分析とは、データからその背後にある価値や知見を得る方法です。これには、データの要約、グラフィカルな表現、統計的な分析、機械学習アルゴリズムを用いたモデリングなども含まれます。
CAEの結果をデータ分析する
一般的にデータ分析には実験データを利用しますが、特に近年、シミュレーションのデータを大量に用意して分析することも増えています。
計算コストが低下し、多数の設計案を一度に評価することができるようになったためです。
多目的最適化やその他の技術もソフトウェアに実装されるようになり、自動的にデータを収集するハイスループット計算などを簡単に行えるようになっています。そのため、多数のデータから有意な知見を得て、重要な考察をすることがCAE技術者に求められています。
どのような分析ツールを使うのか
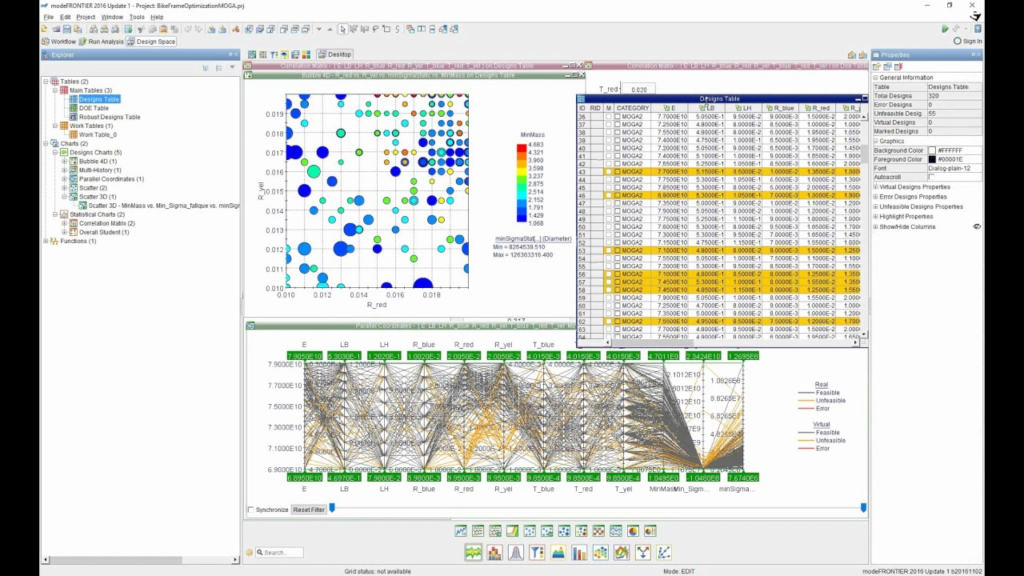
製造業で用いられるデータ分析のツールと言えば、tableauやPower BI、QlikView、KNIMEなどが有名です。
CAE業界で有名なデータ分析ツールにはHEEDS、modeFrontierなどがあります。CAE業界では、CAE計算の自動化ツールに探査アルゴリズムを組み合わせた製品が売り出されており、データ分析ツールもセットになっています。
ただ、このような専門ソフトを使わずとも、エクセルやPythonを用いた分析でも十分な場合もあります。個人的には、使い慣れているツールでトライ&エラーができるものが良いと思います。
分析の目的は結果を得ることではなく、分析の過程で有用な知見が得られることです。そのため、トライ&エラーが素早くできるツールを選ぶことが重要です。
このデータ分析に使える最近の書籍で、本質を捉えたデータ分析のための分析モデル入門というものがあります。
初歩から深層強化学習まで幅広い内容をカバーしています。機械学習について体系的にまとまった本。この本を出発点に各専門書に進んでいくと、理解がスムーズに進みます。
分析に必要なスキルと知識
一般的なデータ分析に必要なスキルは、データ分析ツールを使うスキルがあれば十分です。
重要なのはスキルよりも知恵やノウハウ、経験です。
データの収集方法や分析のアプローチによって生じるバイアスをなくす、不正確なデータや欠損値が多いデータの補正や、分析結果を正確に解釈すること、仮説を立ててデータを分析すること、近似モデルを使うのであればモデルの選択など、ツールを使いこなす以上に経験が重要です。
データ分析の手順
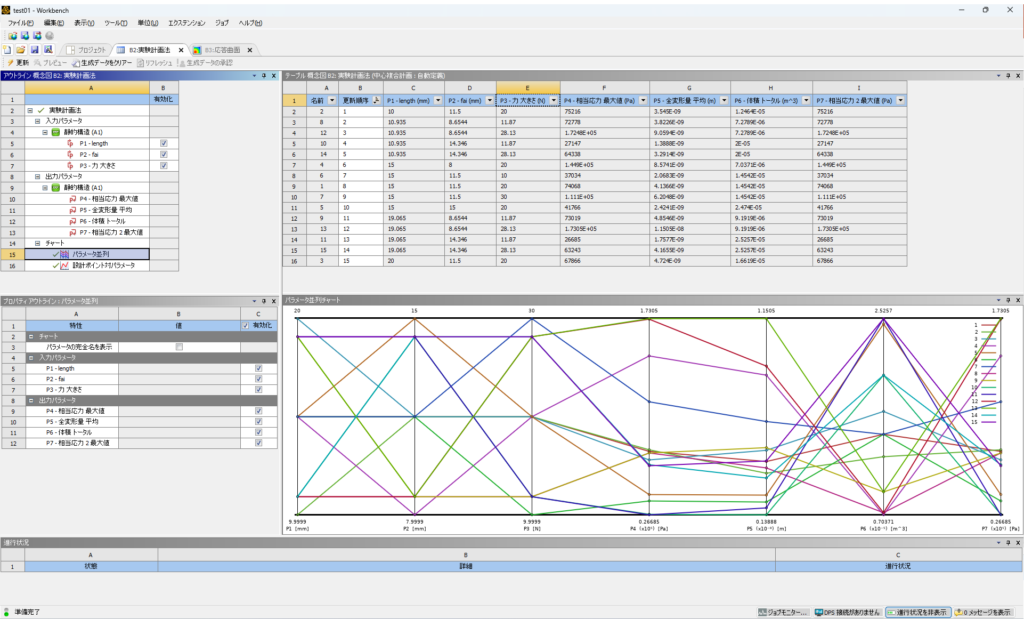
製造業にいるCAE部門でのデータ分析の手順は以下の通りです。
・自分でシミュレーションを回して多数のデータを集める
・データを分析して、製品開発において最も重要な因子が何であるか把握する
・どのような改善が性能を向上させるかを追加で探査する
例えば、車に関しては、できるだけ燃費が良くてコストがかからない車を目指すことが目的です。そのために、どのような構造の車が燃費が良くて軽いのかをシミュレーションを用いて計算し、データ分析を行います。
データ分析の最初に行うべきことは、目的のコストと燃費が目的を達成するかどうかを確認することです。まずはパレート図を書いて、次に「なぜこの設計案は良いのか」という要因を調べます。
因子分析やパラレルプロット、相関行列、寄与率などを求めて、最も効果がある設計値を確認します。
データ分析の結果「そんなの当たり前では」
問題は、シミュレーションが物理法則に基づいているため、シミュレーション結果をデータ分析して分かったことが「そんなの当たり前では」と言われてしまいがちなことです。
ただ、「そんなの当たり前」は誉め言葉で、分かっている現象をシミュレーションで再現できている、ということなので、パラメータの組み合わせによりより良い設計案を見つける(探査する)ことに注力しましょう。
探査の結果「いまの設計案が最適です」
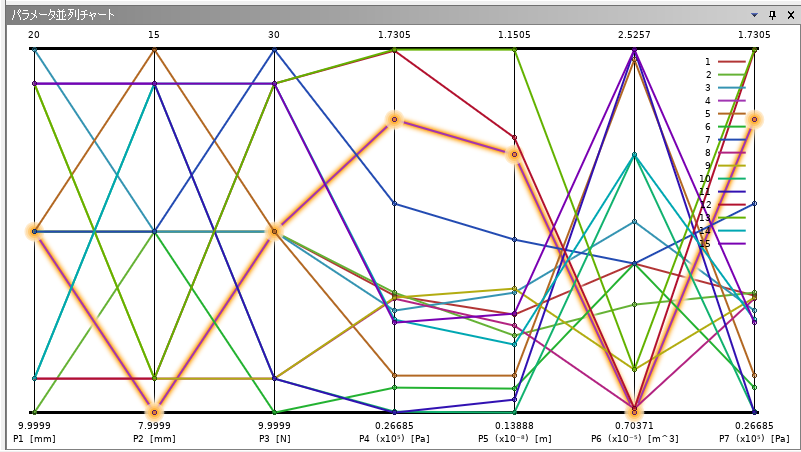
「先人たちが数十年かけてトライ&エラーして見つけてきた設計案が最適だった」「熟練者がカンコツで書いた図面が最強なことが証明された」というパターンもよくあります。
この限界をブレイクスルーするためには、性能の伸びしろを制限しているボトルネックがどこにあるかを確認する必要があります。このために利用できるのがパラレルプロットです。最適化計算に与えている制約条件を広げてやることで、よりよい設計案を見つけらえる可能性が広がります。
制限になっている要因は、量産に必要な金型の条件、コスト、他の部品との関連など、多岐にわたります。これらは、社内外との調整になることもあります。
まとめ
近年、CAE結果が膨大になりつつあり、それらを分析して知見を得ることが必要になりつつあります。
分析ツールはこだわる必要はなく、シミュレーションの結果を分析してみることで、新たな知見が得られる可能性があります。
一方で、分析しても「当たり前のことしかわからない」「今の図面が最適な設計案だった」など、成果が挙がらないこともあります。
筆者はそれでもめげずに、様々な試行錯誤を繰り返して、有用な知見を得るための旅を続けています…。
コメント