電気自動車(EV)の普及には、高性能なモーター技術が不可欠です。プロテリアル(旧日立金属)は、EV向けモーターの消費電力を最大5%改善できる新しい合金材の製法を開発し、2025年に量産を目指しています。
新合金材は、現在主流の電磁鋼板に比べてエネルギー損失を大幅に抑えることができ、これによりモーターの高回転化や小型化を実現できるとのことですが、プレスリリースの範囲では読み取れる情報に限界があります。
本記事では、プロテリアルのモーター材料「アモルファス合金」の何が凄いのかを解説します。
アモルファス合金はモーター向きではない
電磁鋼板 | アモルファス合金 | |
---|---|---|
鉄心損失 | 損失大きい | 損失小さい (高効率) |
厚み | 厚い | 薄い (電磁鋼板の1/10) |
加工性 | 〇 | × |
硬さ | 比較的柔らかい | 硬い (電磁鋼板の5倍) |
特徴 | モーターコアに利用 | 薄く加工しにくいためモーターコアとして不向き |
モーターコア材料には、一般に電磁鋼板が用いられます。
電磁鋼板の限界を超える高効率モーターを実現する材料として、鉄心損失の低いアモルファス合金が注目されていますが、アモルファス合金は硬く加工が難しく、かつ素材が薄いためにモーターコアに使うには不向きで、量産モーターコアへのアモルファス合金の適用は困難とされていました。
鉄心損失(鉄損)とは、電磁鋼板やアモルファス合金などの磁性材料が、電磁エネルギーを熱エネルギーへ変換する際に生じるエネルギー損失のことです。アモルファス合金は鉄損が非常に低いとされ、電気モーターや変圧器などの効率を大幅に向上させることができます。
プロテリアルの技術は何が凄いのか?
プロテリアル(旧日立金属)は、複数枚のアモルファス合金を連続的に積層接着する技術を開発し、薄いアモルファス合金を厚い材料に加工できるようにしました。接着剤を薄く均一に形成する独自の技術を用いて、高い占積率*を実現しています。
積層接着の実現のために、プロマテリアルは以下の技術開発を実施したと発表しています。
- 接着剤の選定
- 接着層の厚みの制御
これらの技術開発の詳細については開示されておらず、プレスリリースでも触れられていません。以下では、一般的に接着剤の選定と接着剤厚みの制御に必要な技術開発について述べます。
接着剤の選定
モーターコア用アモルファス合金の接着剤には、高い接着強度と耐熱性、電気絶縁性が求められます。熱伝導性もひとつの指標です。最も重要なのは接着強度で、モーターの運転中に発生する振動や熱変化にも耐えることができる強固な接着を保持する必要があります。
接着剤の選定は、接着剤の粘性(ドロドロ具合)や硬化特性(固まる速度など)が指標になります。接着剤の粘性が適切であれば、より薄い層の形成が容易になります。硬化特性の改良も必要で、積層材料間の強固な結合を確保することができます。
アモルファス合金に表面処理を行い、接着剤が均一に広がりやすい表面特性を作り出す技術も必要です。表面エネルギーを調整することで、接着剤の均一な広がりやすさを向上させます。
接着層の厚みの制御
接着層の厚みの制御のためには、精密な塗布技術が必要です。スピンコーティングやドクターブレード法、ディップコーティングやインクジェット塗布などの方法で接着剤を塗布するわけですが、これらの塗工条件の最適化や、独自のノウハウを蓄積していきます。
同様に、リアルタイム膜厚測定など、製造プロセス中での分析技術も必要となりますし、塗布環境(温度、湿度など)を厳密に制御する必要もあります。こういった「地道な技術開発」により、プロマテリアルは、アモルファス合金の接着と厚み増を実現していると考えられます。
利用できるモーターが広がる
モーターには、ラジアルギャップ型(最もよく用いられる)とアキシャルギャップ型のモーターがあります。
アモルファス合金は、アキシャルギャップ型モーターには既に使用されていましたが、その硬度が高く素材が薄いために、量産に適したラジアルギャップ型モーターコアへの適用は困難とされていました。プロマテリアルは、接着技術によってこのハードルを突破したわけです。
アモルファス合金とは?
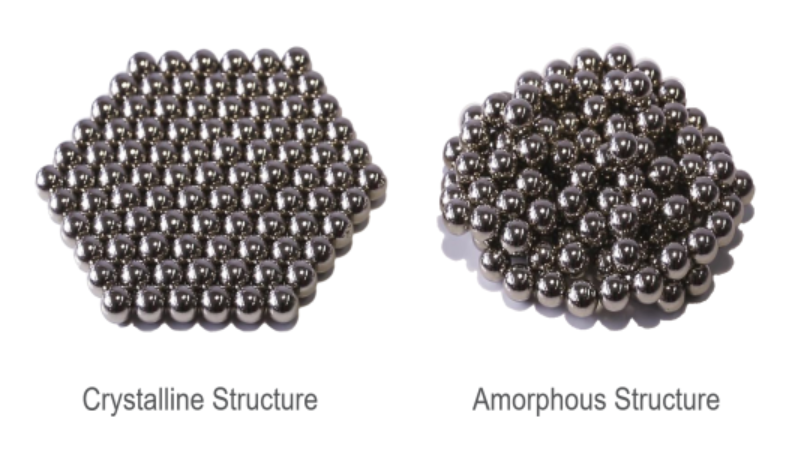
アモルファス合金(Amorphous)は、結晶構造を持たない非晶質の金属材料です。通常、金属は冷却過程で結晶格子構造を形成しますが、アモルファス合金は急速冷却などの特殊な製造過程を経ることで、その結晶化を防ぎ、原子が不規則に配列したガラス状の構造を持つ材料を得ます。
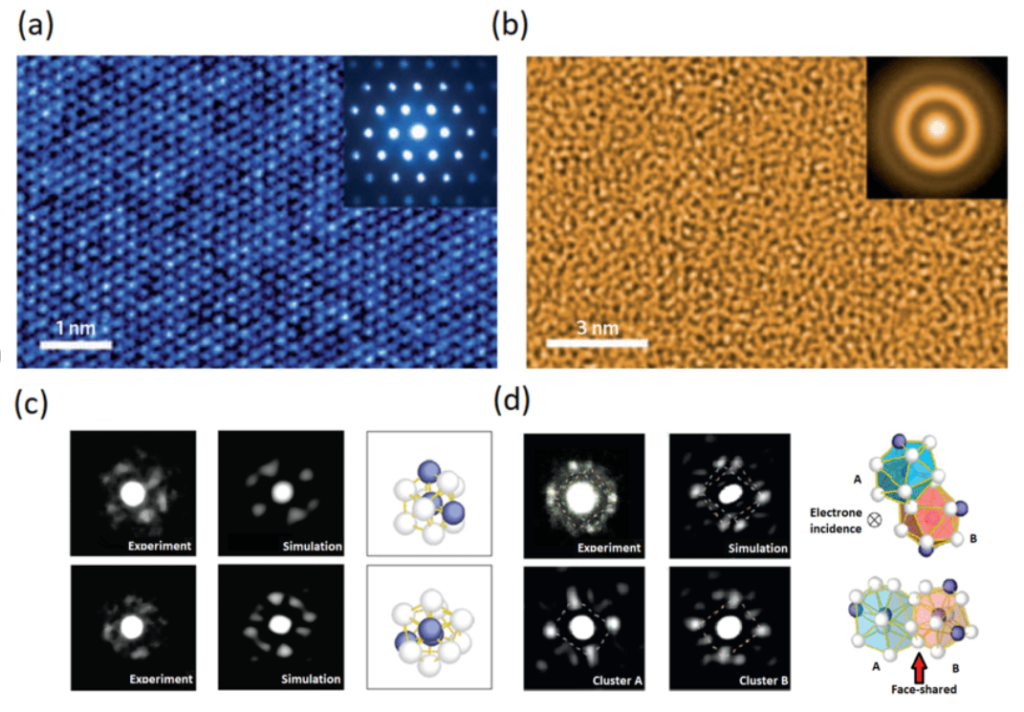
アモルファス合金は、一般に金属を非常に高い速度で冷却(急速凝固)することによって製造されます。溶融した金属を秒速で2000℃から100℃程度まで冷却する必要があります。この高速冷却により、原子が結晶格子を形成する前に固化し、非晶質(結晶構造を持たない)状態が保持されます。急速凝固プロセスにより、金属が固体化する前に結晶化するのを防ぎ、非結晶構造が形成されます。例えば、溶融した金属を薄いリボン状にして、急速に冷却する方法があります。
この急速凝固プロセスを効率的に行うためには、溶融金属を非常に薄いリボンや薄板にすることで冷却速度を高める必要があります。分厚い板はなかなか冷えないですが、薄い板ならば急冷が可能です。背反として、アモルファス合金の厚板を製造することが困難になります。
なぜアモルファス合金は鉄心損失が小さいのか?
アモルファス合金の鉄損が小さいのは、アモルファス合金が非晶質(結晶構造を持たない)状態であるため、ヒステリシス損が少なく、また、薄いリボン状に加工されることで渦電流損を効果的に低減できるためです。
ヒステリシス損は、磁性材料が磁化される際に生じるエネルギー損失の一種です。磁性体に外部から磁場を加えると、その材料は磁化されますが、この磁場を取り除いた後も、材料は完全には元の状態に戻らず、ある程度の磁化状態が残ります。この現象を磁気ヒステリシスと呼びます。磁場を加えて磁化し、その後磁場を減少させて再びゼロに戻す過程で、材料は異なる磁化のパスをたどります。この磁化と逆磁化のプロセスでエネルギーが熱として失われることをヒステリシス損と呼びます。
モーターの種類
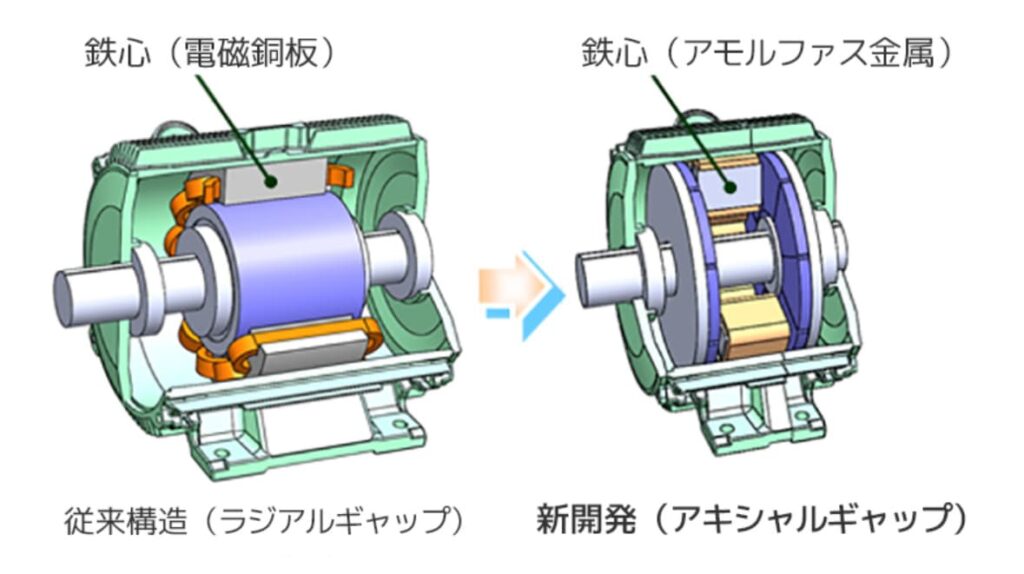
モーターには、ラジアルギャップ型(最もよく用いられる)とアキシャルギャップ型があると説明しました。それらをもう少し詳しく解説します。
ラジアルギャップ型モーター
ラジアルギャップ型モーターは、最も一般的なモーターの形式で、磁場がローターの中心から外周に向かって放射状に広がる(ラジアル方向に広がる)構造をしています。このタイプのモーターでは、ステーター(固定部分)とローター(回転部分)の間の磁気的な隙間(ギャップ)が放射状に配置されています。
- 製造が容易(大量生産に適する)
- コンパクトで効率的な設計が可能
- 家電製品や産業用機械、自動車などで利用
アキシャルギャップ型モーター
アキシャルギャップ型モーターでは、磁場がモーターの軸方向(アキシャル方向)に広がります。このタイプのモーターでは、ステーターとローターが平行な平面上に配置され、磁気的な隙間が軸方向に形成されます。
- 薄型で軽量な設計が可能で、空間効率が良い。
- ユニークな設計により、特定の応用分野で高い性能を発揮。
- 冷却が効率的で、高出力密度を実現可能。
フェライト磁石も開発する
ネオジム磁石 | フェライト磁石 | |
---|---|---|
重金属 | テルビウムやジスプロシウムを利用 | 重金属フリー |
重量(密度) | 重い 約7.3~7.5 g/cm³ | 軽い 約4.8~5.0 g/cm³ |
磁力(最大エネルギー積) | 非常に強い 約30~52 MGOe | 弱い 約1.1~4.5 MGOe |
コスト | 高い | 低い |
プロテリアルは、モーター材料としてフェライト磁石も開発しています。フェライト磁石はモーターコアではなく、永久磁石として機能し、ステーター(固定された部分)から供給される電気エネルギーを機械的な動きに変換するために使用されます。モーターの設計において、フェライト磁石はローター部分に取り付けられることが多く、回転する部分に磁場を提供します。
フェライト磁石は、モーターに必要だった希少資源の重希土類を減らした金属材料です。従来のネオジム磁石と異なり、テルビウムやジスプロシウムという重希土類を使わずに済み、中国依存度が高い重希土類をサプライチェーンから切り離すこともできます。
まとめ
アモルファス合金は、その低い鉄心損失(鉄損)により高効率モーターの実現が期待されていますが、硬さと薄さから加工が難しく、従来はモーターコアには不向きとされていました。プロテリアルは複数枚のアモルファス合金を連続的に積層接着する技術を開発し、接着剤を薄く均一に形成することで高い占積率を実現しました。
プロテリアルの技術開発は、モーターコア材料としてのアモルファス合金の利用可能性を広げています。今後のEV普及に一役買う、重要な技術と言えます。
関連記事
コメント