近年、エネルギー貯蔵技術の進歩は急速なものとなり、電気自動車や再生可能エネルギーの普及を促進しています。その中でも、注目を浴びているのが全固体電池です。
全固体電池は、従来の液体電解質を固体電解質に置き換えることで、高い安全性とエネルギー密度を実現する革新的なバッテリー技術です。
全固体電池の実用化へのハードルは主に製造プロセスにあるとされていますが、その製造方法はあまり知られていません。
本記事では、全固体電池の製造方法について詳しく紹介します。
全固体電池とは
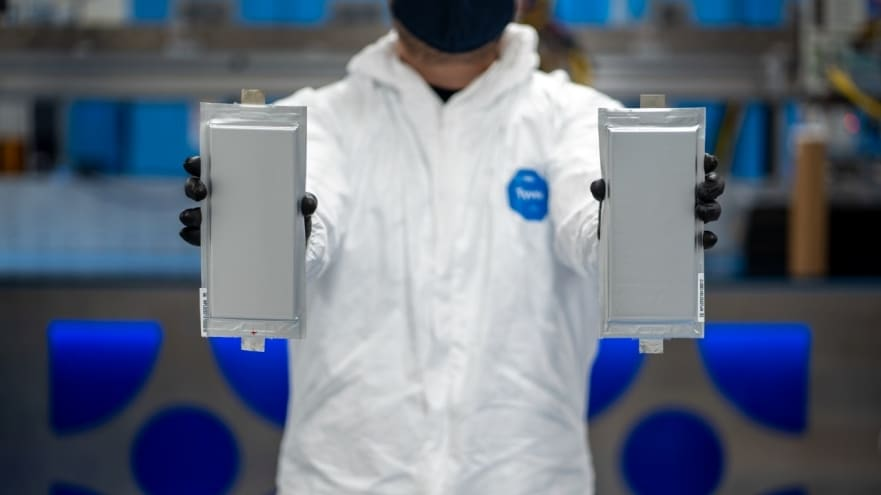
全固体電池は、液体電解質ではなく固体電解質を使用することで、高い安全性とエネルギー密度を実現したバッテリーです。固体電解質はイオンの通り道として機能し、バッテリー内部でのイオンの移動を可能にします。この特徴により、全固体電池は高い耐久性と長寿命を備えています。
全固体電池の製造プロセス
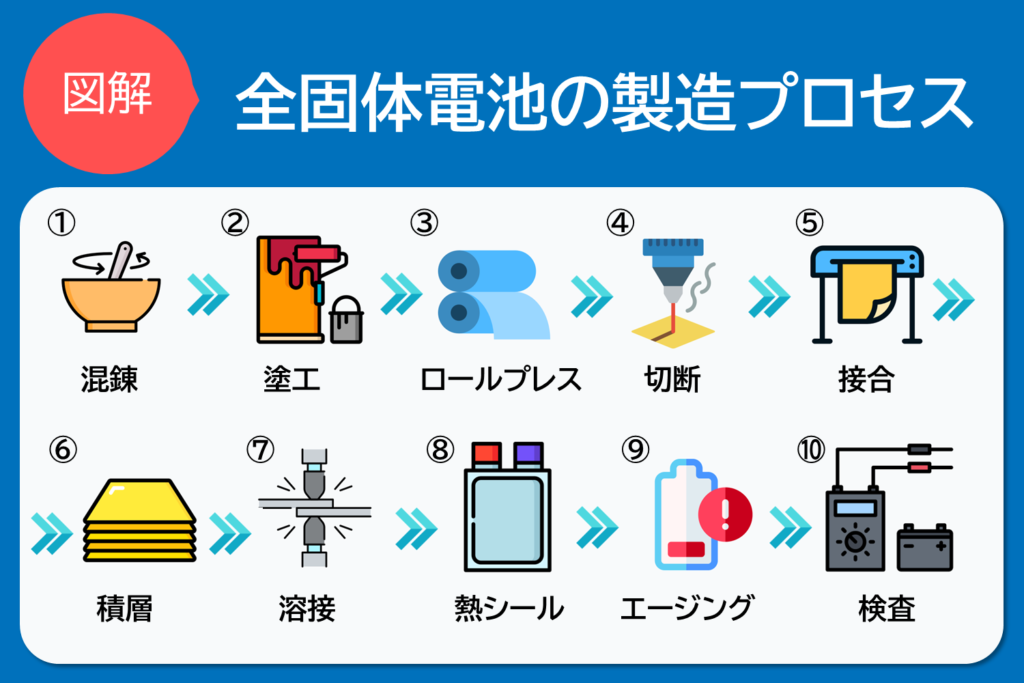
全固体電池の製造プロセスは、主に以下のフローで行われます。
- 電極材料の混錬
- 電極の塗工
- ロールプレス
- 電極の切断
- 電極の接合
- 積層
- 集電泊の溶接
- 熱シール
- エージング
- 検査
それぞれの工程について、詳しく紹介します。
電極材料の混錬
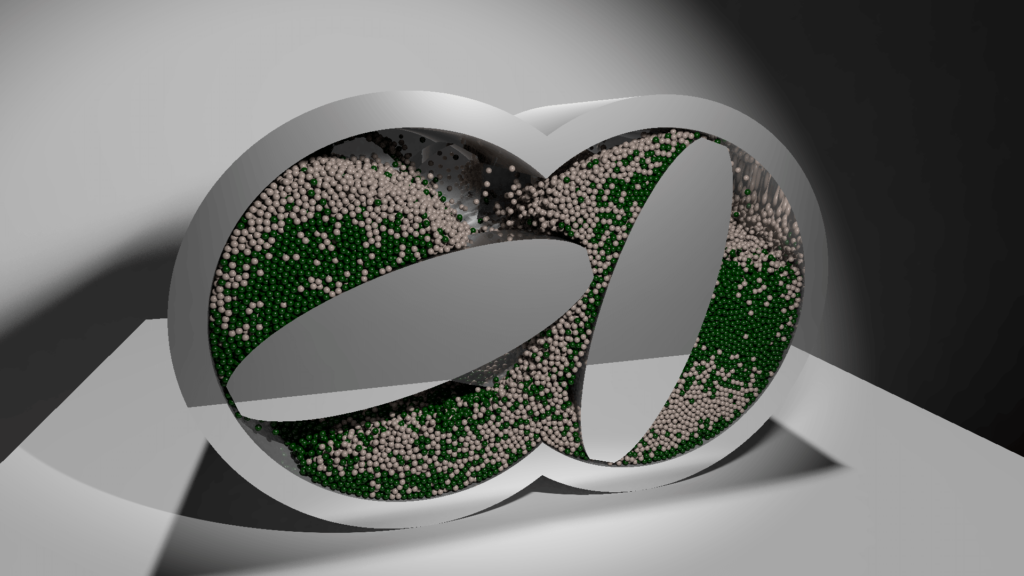
全固体電池の製造過程では、まず活物質(バッテリーメタル)、導電助剤、結着材(バインダー)、固体電解質を混ぜ合わせる工程があります。
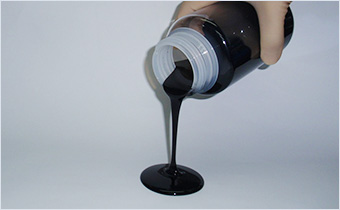
この混錬では、高い均一性と混合効率が求められます。均一な混合を実現するために、分散溶媒を使用してスラリー(黒い溶液)を作成します。
電極を塗工する
混錬された材料を、金属箔などの基材に塗工します。
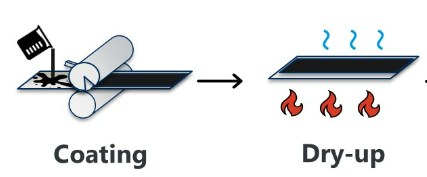
塗工後は、乾燥させる必要があります。しかしこの過程では、厚みや均一性の制御が困難な課題があります。電極の均一な塗工を実現するためには、高い技術が求められます。
電極をロールプレス
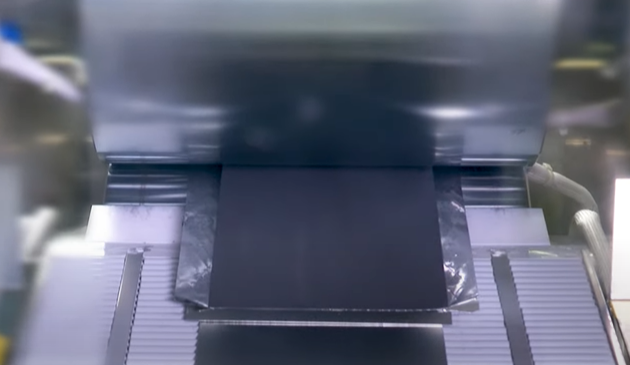
塗工された電極は、圧縮されて表面を滑らかにするためにロールプレスされます。この工程では、厚みの調整や固体材料同士の接触面積を向上させる必要があります。電極の均一な厚みと圧力制御は、バッテリー性能に直結する重要な要素です。
電極の切断
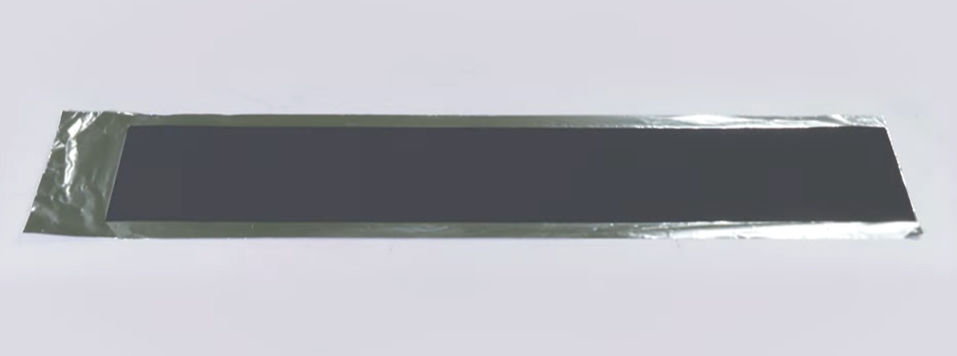
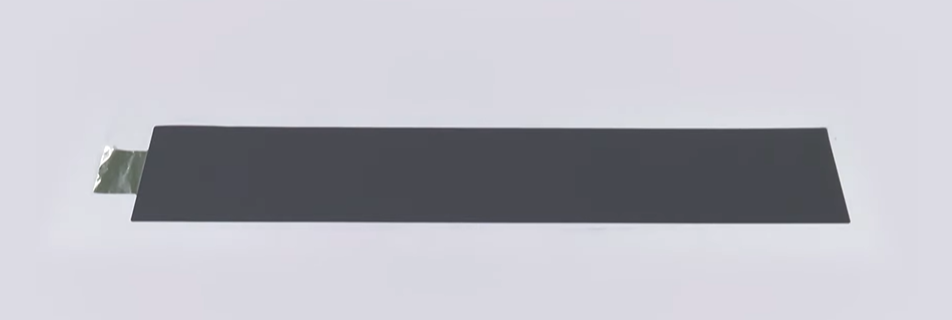
ロールプレスされた電極は、所定の寸法に加工する必要があります。正確な寸法での切断が求められます。この過程では、高い精度と制御が必要とされます。
電極と電解質の接合
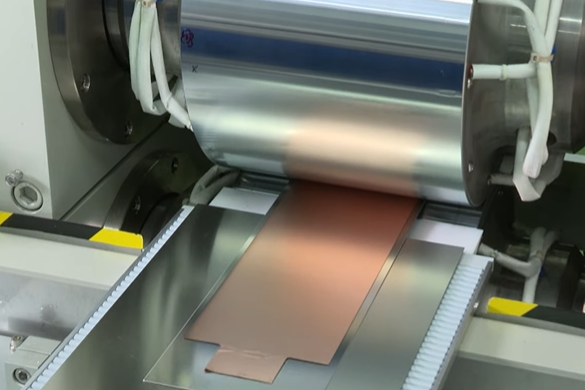
全固体電池では、正極と負極を接合する必要があります。この接合は、高い接合強度と均一性が求められます。正確な位置合わせと抵抗をなるべく小さくするためには、高度な技術と品質管理が欠かせません。
積層する
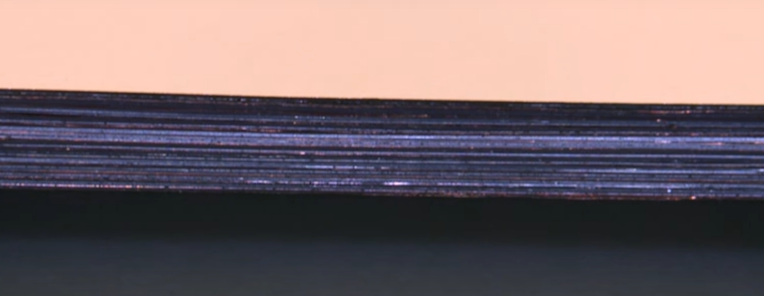
電極と電解質を複数積層して全固体電池を作ります。しかし、均一な積層と圧力制御は困難な課題です。積層過程では、バッテリーの性能や寿命に影響を与える可能性があるため、高い品質管理が不可欠です。
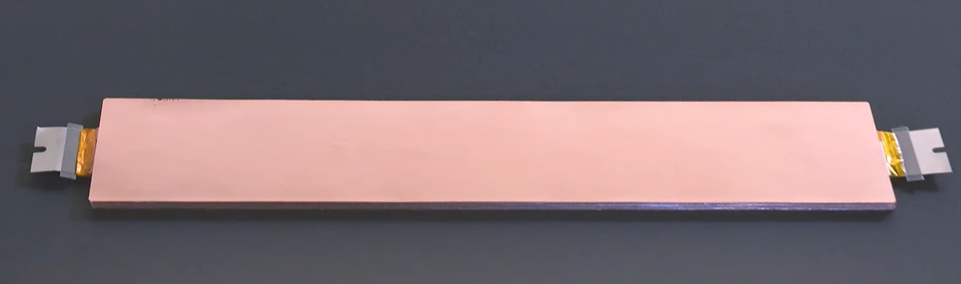
積層後のバッテリーの全容です。このあと、集電端子を溶接し、積層物をパウチでパッキングすることで、見慣れた全固体電池の形となります。
集電端子の溶接
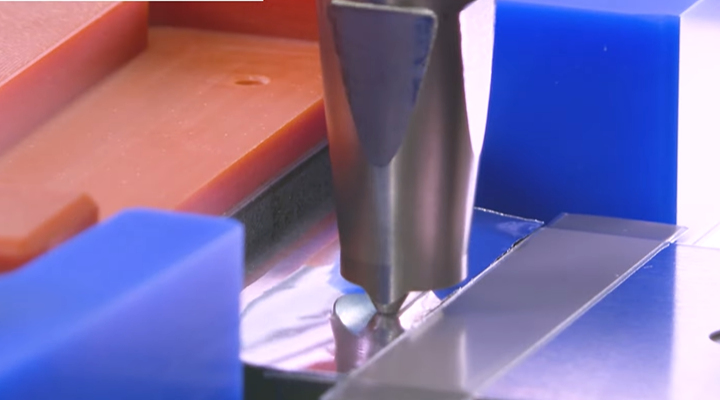
全固体電池には、集電端子として機能するタブを溶接します。これにより、電気の集電が可能となります。タブと電極の正確な位置合わせと抵抗を小さくするための溶接は、技術的に困難な課題です。
熱シーラーでセルを溶着
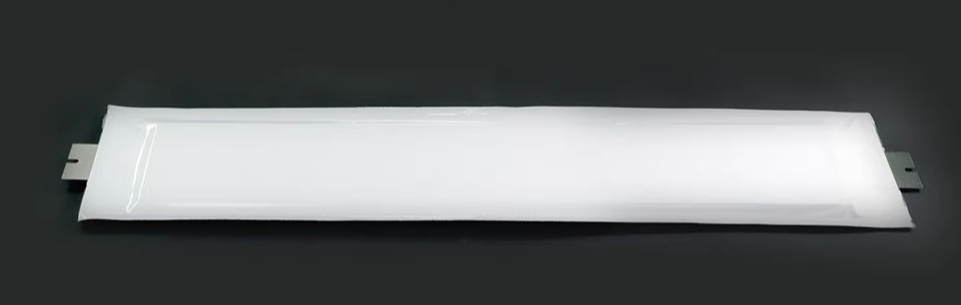
電池をラミネートに入れて封をするために、熱シーラーを使用します。この過程では、高い密閉性と耐熱性が求められます。適切な封を行うことで、バッテリーの安全性と性能を確保することができます。
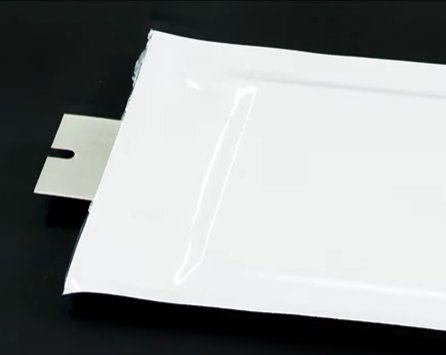
熱シールされた全固体電池は、このあとエージング処理と検査を経て出荷されます。
エージング
全固体電池は、安定した性能を得るためにエージング(熟成)が必要です。時間と温度を管理しながら、バッテリー内部の化学反応や結晶構造の安定化を促進します。エージングにより、バッテリーの性能が最適化されます。
検査
最終的に、製造された全固体電池は充放電容量、劣化状態などの性能を測定するために検査が行われます。高精度な測定技術と多様なパラメータの評価が必要とされます。これにより、バッテリーの品質と性能を確認し、最終製品の出荷準備が行われます。
まとめ
全固体電池の製造方法を紹介しました。
製造工程には、均一性の確保、厚みの制御、接合の品質、積層と圧力制御など、各工程においてさまざまな技術的課題が存在します。しかし、これらの課題を克服することで、高性能なバッテリーを実現することができます。
全固体電池の製造方法の改善に向けた研究や開発は、持続可能なエネルギー貯蔵技術の進歩に大きな影響を与えると考えられています。日本の自動車メーカーは2028年頃から全固体電池の投入を予定しており、全固体電池の実現に向けて、より効率的な製造プロセス、高品質な製品の提供、コスト削減などに取り組んでいます。
関連記事
コメント