テスラは、EVの製造・販売における業界の常識を塗り替え続けています。今後、テスラが実現する技術の中で最も注目すべきなのが、「unboxed process(アンボックスドプロセス)」です。
この記事では、従来の製造工程と比較しながら、unboxed processの特徴やメリット、デメリットについて解説します。
Unboxed Process(アンボックスドプロセス)とは
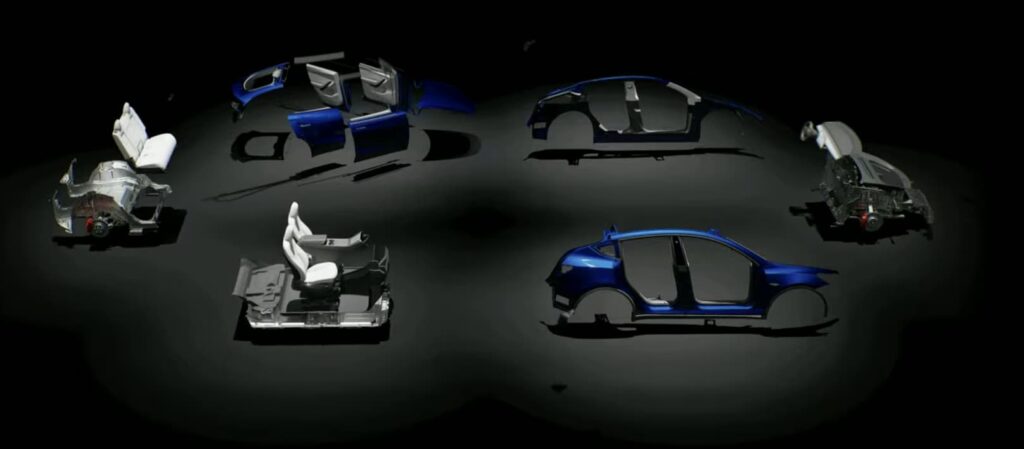
Unboxed Process(アンボックスドプロセス)は、車の車体をいくつかの大きなモジュールに分けて別々に組み立てておき、最後に合体して車を製造する方法です。
従来の自動車組み立ては、車両に数万点の各部品を取り付ける方法で行われてきましたが、この方法では並列化が困難で、自動車製造の工程を短くするための1案をテスラが提示したのです。
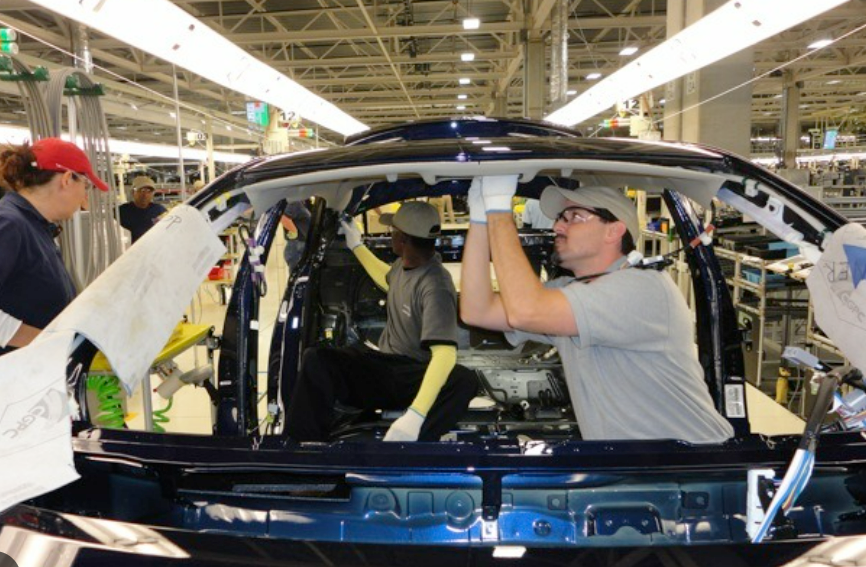
自動車は、ボディを先に製造し、その中に人が乗り込んで部品を取り付ける方法で製造されています。この「箱(box)」があるために組み立てに時間がかかると考えたテスラは、「箱なし(unbox)」とする方法を考え出したのです。
車をいくつかのモジュールに分けて、それぞれのモジュールを高い完成度まで組み立て、最後にすべて合体すします。それぞれのモジュールを並列で製造することで、組み立ての時間が大幅に短縮されるとのことです。
この手法は自動車業界で多いに注目されており、トヨタ自動車もUnboxed Processをまねた製造工程を目指すとしています。
従来の製造工程
Unboxed Processの詳細を解説するまえに、従来の自動車工程を見てみます。
自動車の製造工程は、ヘンリー・フォードが100年前の1922年に導入した考え方に基づいており、一般的な自動車製造では、以下のような工程が順番に行われます。
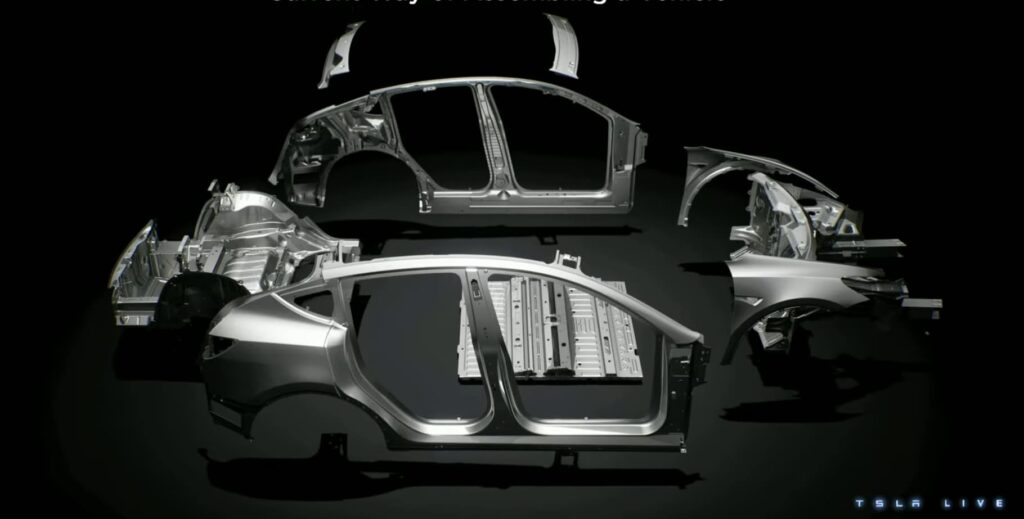
まず、何百もの個々の部品をロボットで溶接してボディを形成します。
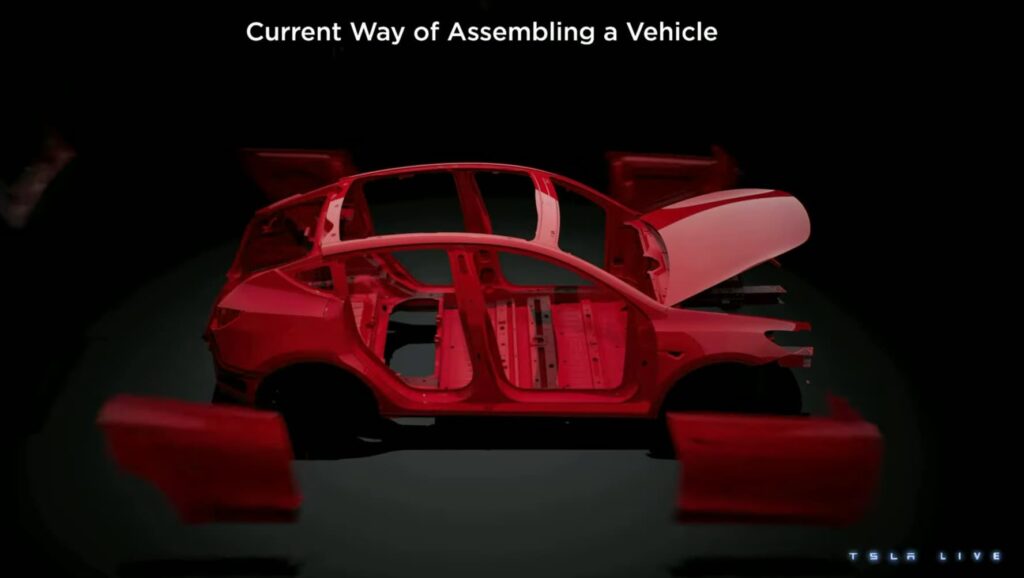
次に、ボディに塗装を施します。すべての部品が同一成形色となるよう、ドアパネルも含めてこの工程で塗装します。
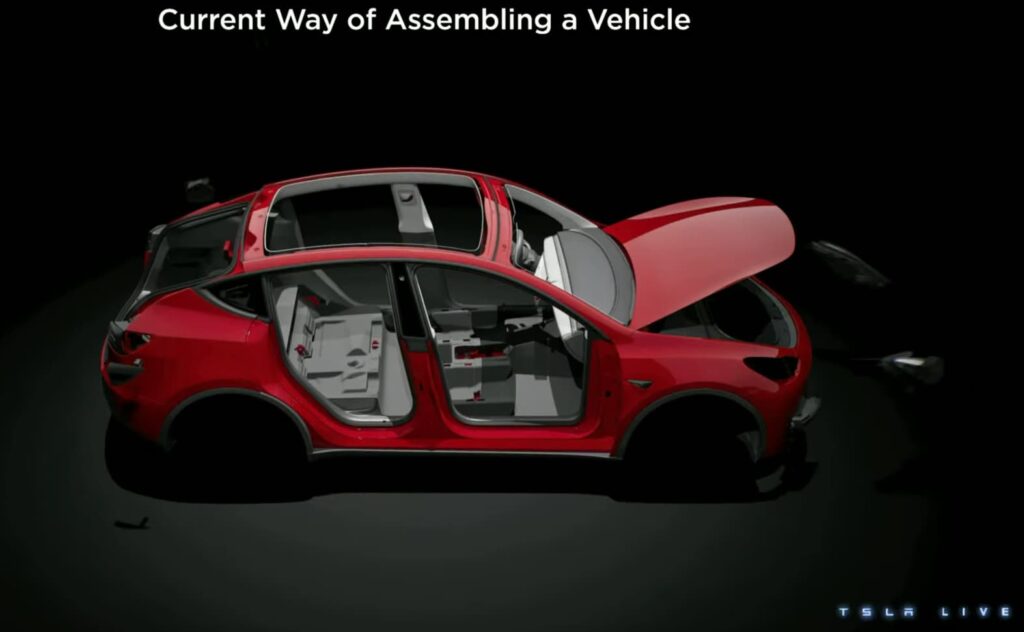
内装および電装部品を組付けます。シートやドアパネル、電気系統などの内装および電装部品を組み付けます。
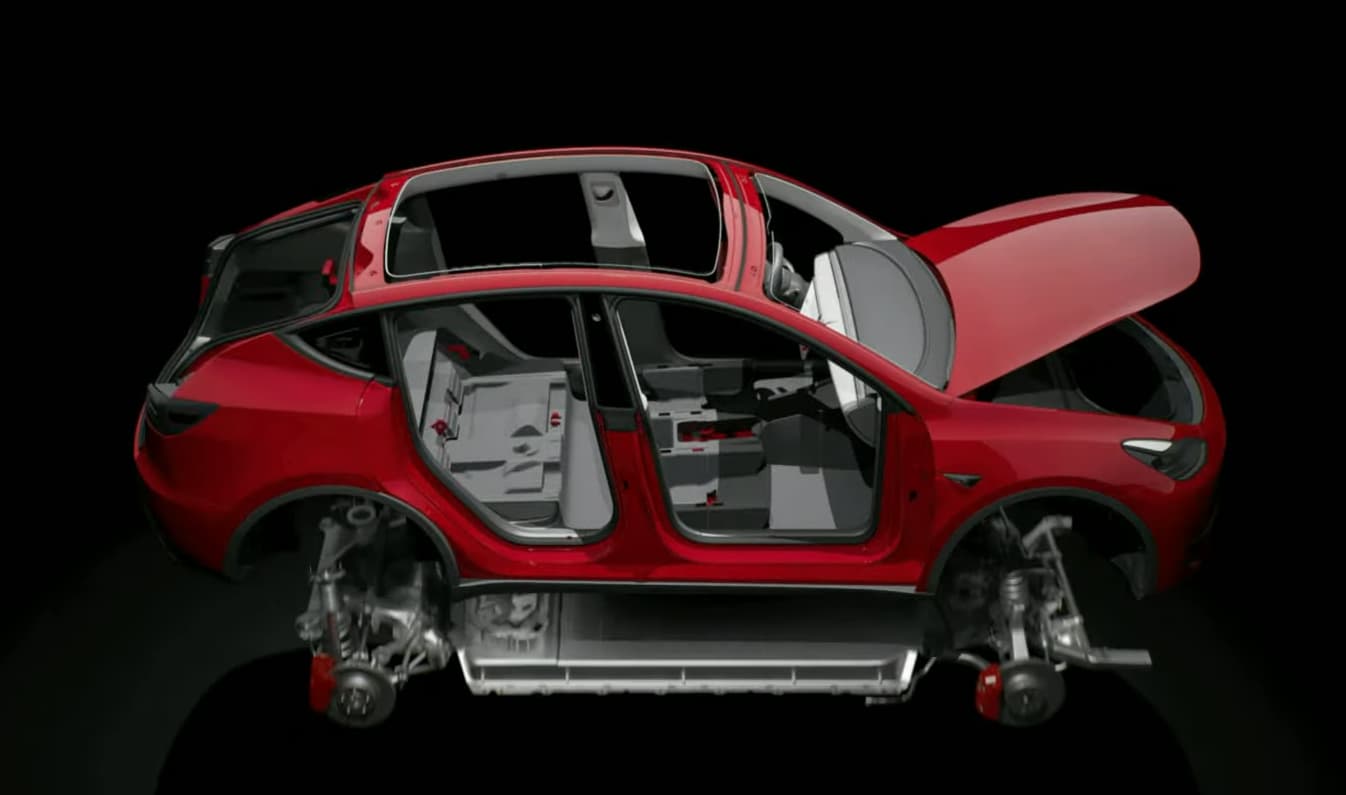
エンジン、サスペンションなどのシャシー関連の部品を組み付けます。
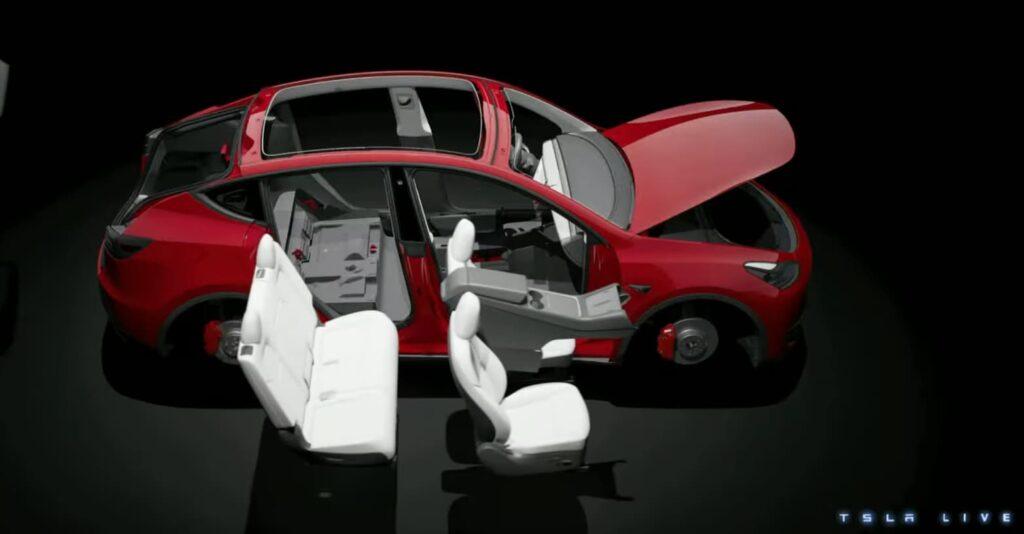
シートを取り付けます。機械を併用しながら、人の手で固定していきます。
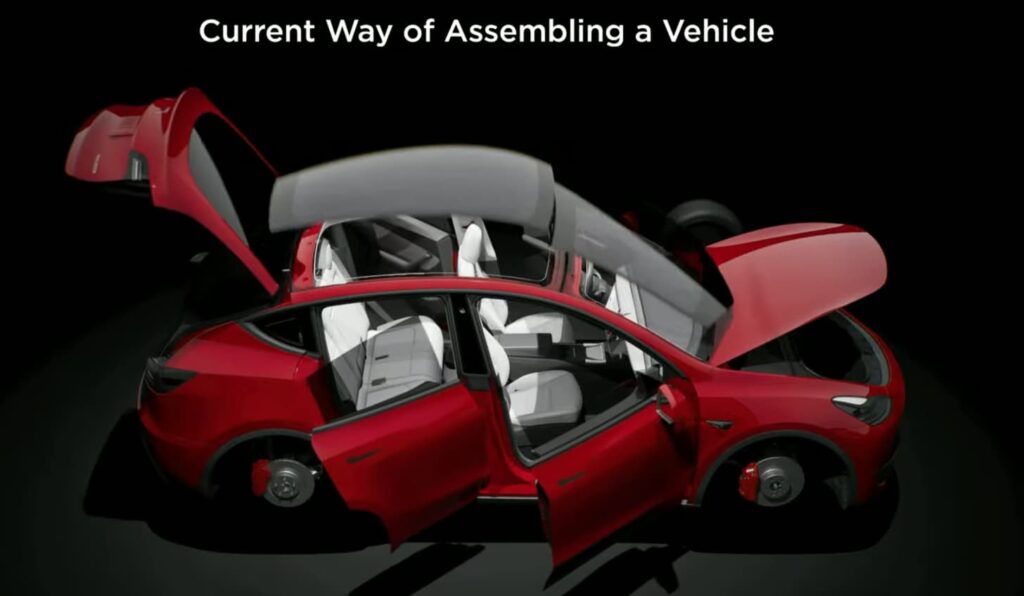
ドアやハッチバックなどのドア関連の部品を組み付けます。
このように、従来の自動車製造工程は、車両に順番に部品を取り付けて製造しています。これはテスラも例外ではなく、もちろんトヨタなどの既存のOEMもこの方法で自動車製造を行っています。
従来工程の課題
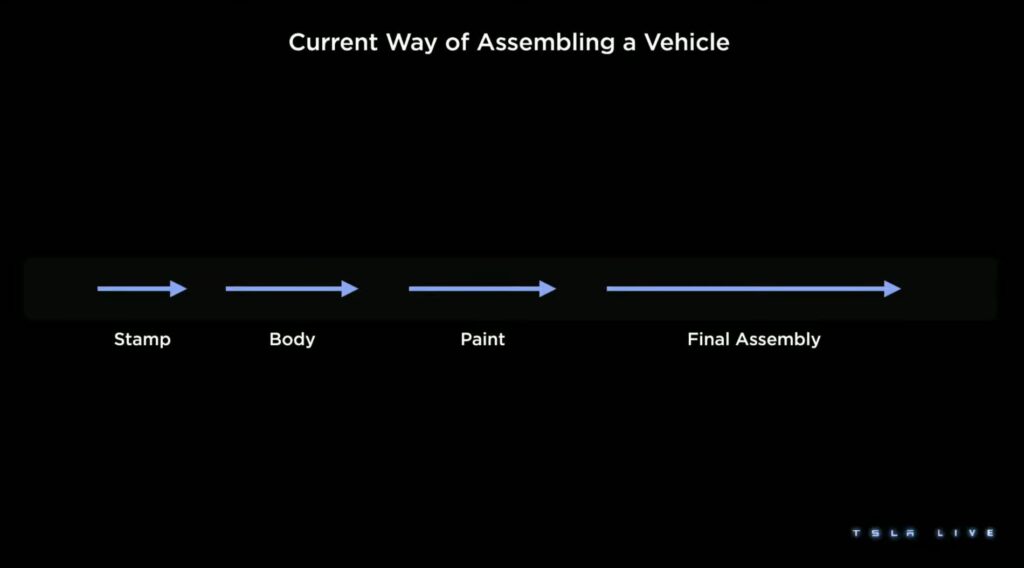
従来の製造工程では、車両を部品ごとに組み立てていくため、直列のプロセスとなります。
直列の工程では作業が並列で行えず、リードタイム(作業時間)が長くなるという課題があります。複数の部品が一度に組み立てられないため、工場全体でみたときの効率(生産性)が低くなります。
Unboxed Process
テスラの提唱するunboxed processは、車両をある程度まとまった部品単位である「モジュール」に分けて別々に造り、それらを一体化して1台の車両に組み立てる方法です。
具体的には、以下の手順で行われます。
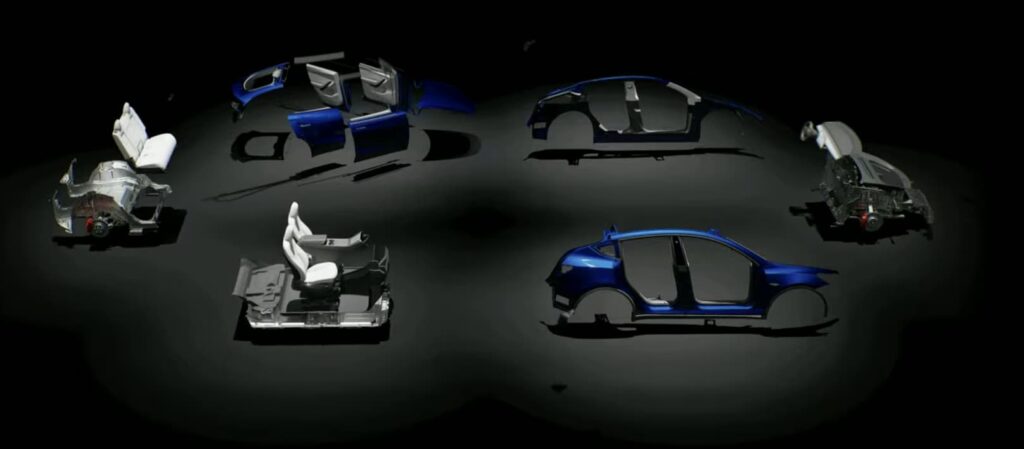
車両をフロント、リア、フロア(シートを含む)、サイドパネルの主要なサブアセンブリに分割し、それぞれを個別に組み立てます。
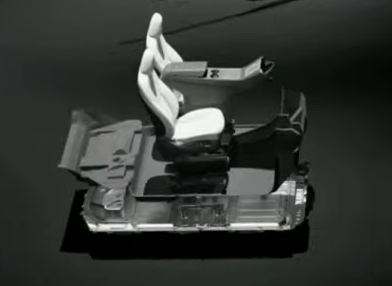
たとえば、シートや内装部品を車両ではなくバッテリーパックに組み付けることで、直列でしか作業できなかった部分を並列化します。
これらの6つのモジュールの組み上げを同時に進めることで、効率的な生産が可能となります。
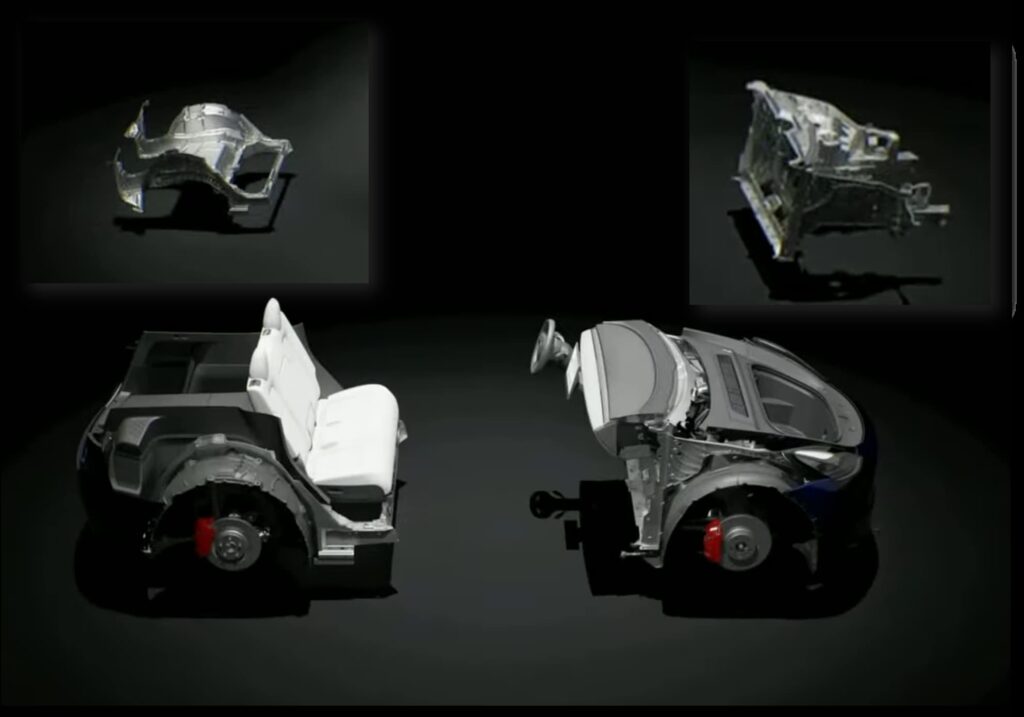
ボディは巨大な一体鋳造品であるギガキャストを使用して製造されます。
このボディにサスペンションやモータなどの足回りを直接組み付けています。
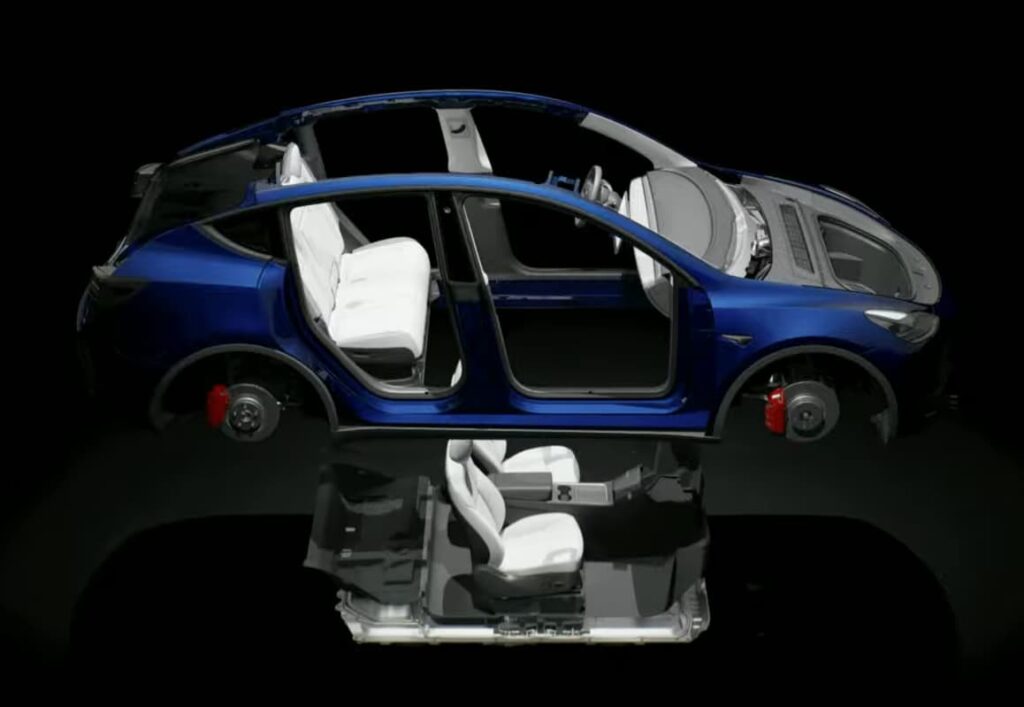
別々に組み立てた6つのアセンブリを、1つの車の形に組付けます。
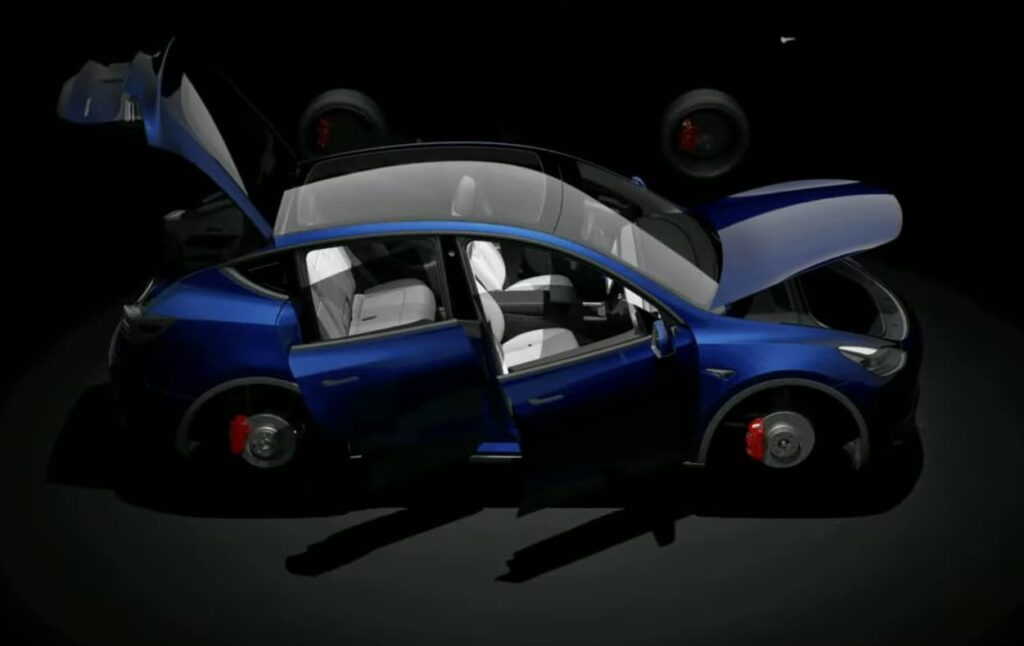
最後に、ルーフやボンネット、ドアやタイヤなどの部品を組み付けて完成です。
事前に多くの作業を別工程で行っておくことで、最終的な組付けラインの工程を大幅に減らすことができます。
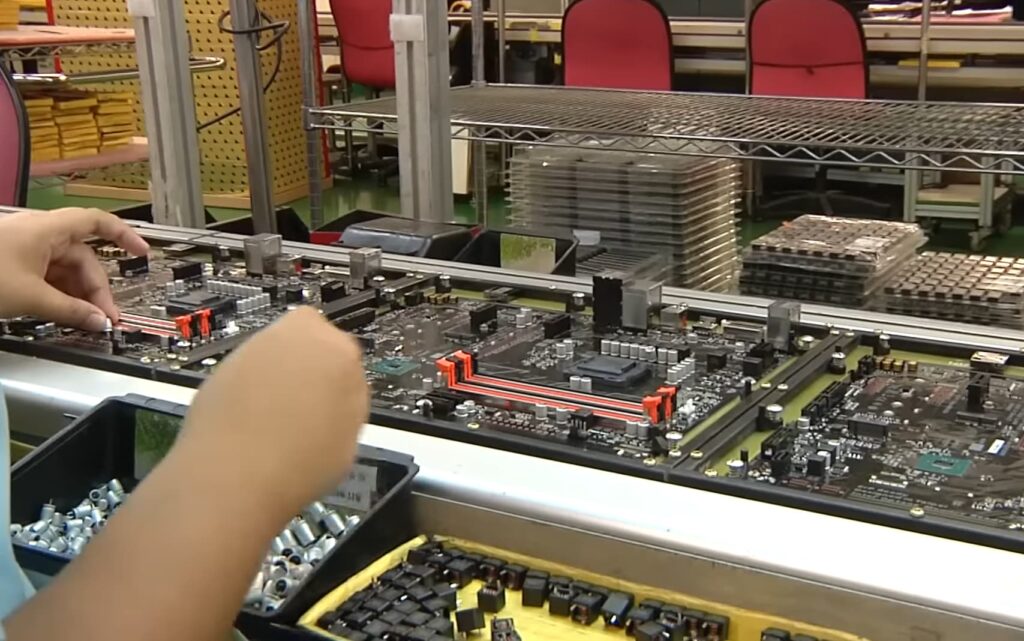
unboxed processの思想は、パソコンなどに近いものです。パソコンは部品の標準化が進んでおり、部品同士の接合や接続部分のインターフェースまでが規定されているため、部品を簡単に組み合わせるだけで完成品に組み上げることができます。
自動車に置いても、このようなモジュラー型の製造が進めば、製品の価格が急激に下がり、普及の加速に寄与することになります。EV部品の共通化は、鴻海などの企業がプロジェクトを進めており、unboxed processの浸透により更に進歩する可能性があります。
組み立て方はガンプラに似ている
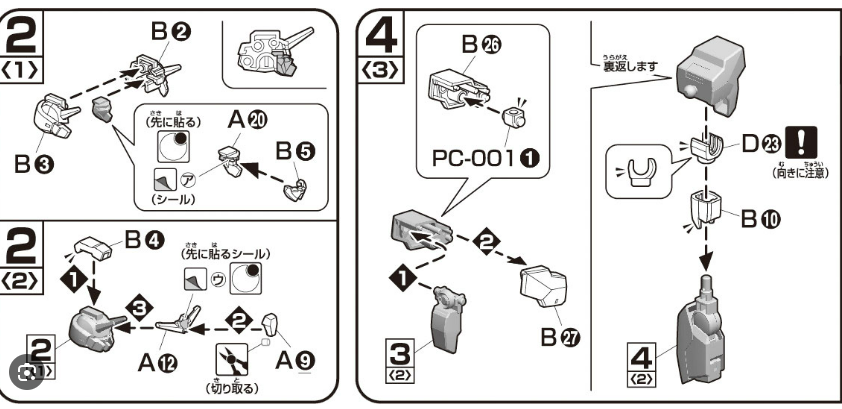
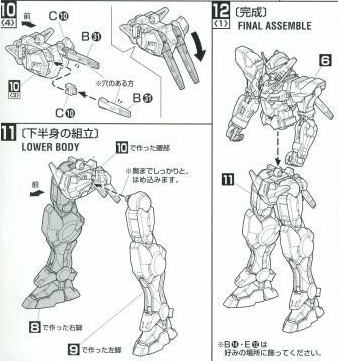
Unboxed Processの製造プロセスは、ガンダムのプラモデル(ガンプラ)に似ています。
ガンプラは、腕や足、動体や頭部、武器といった部品を個別に組み立てておき、最後に合体してガンダムの形になります。
これを車でやっているのがUnboxed Processです。
unboxed processのメリット
unboxed processの最も大きなメリットは、工程短縮とコストの削減です。
工程の短縮とコスト削減
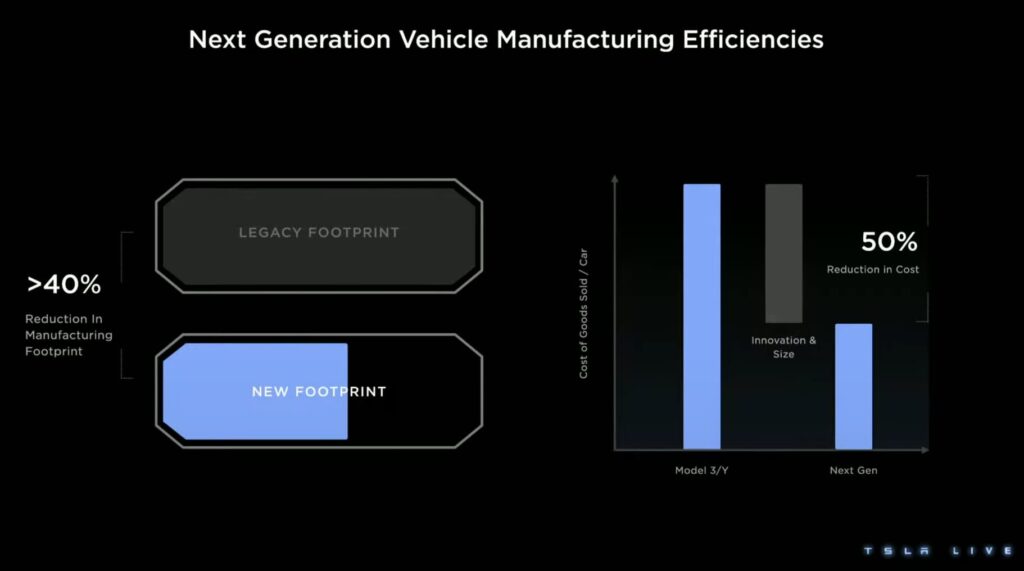
unboxed processでは、従来の方法よりも工程を40%以上減らすことができ、コストを50%下げることができるとされています。工程とは、製品を完成させるための作業ステップであり、一般的に工程が減れば、自動車製造に必要な時間も少なくなります。
スペース効率の向上

バッテリーにシートを直接組み付けるなど、小さなモジュールから作業を行うことで、作業者の移動範囲が減り、スペースの効率を上げることができます。
工場の広さは有限で、広いスペースを使う工程ほど、コストがかかります。なるべくコンパクトな工程を組み合わせることで、全体として生産効率を向上させることができます。
生産ラインのコンパクト化により、工場や生産ラインの新設・増設時にも、初期投資費用を抑えることができるだけでなく、工場建設時の工期も短縮できます。
工程構造の並列化が可能
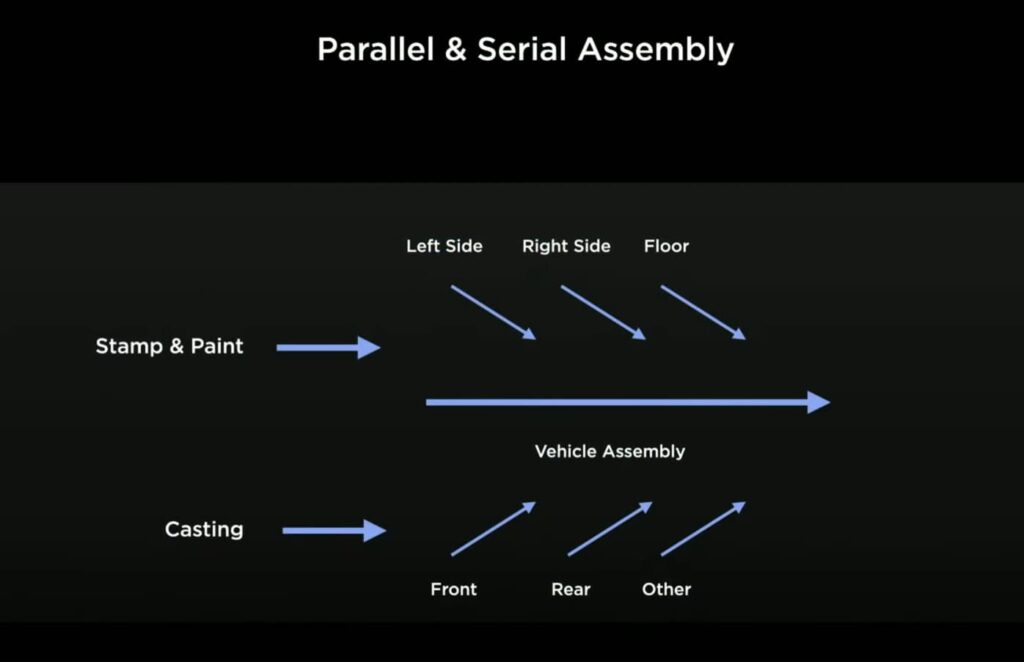
unboxed processは”サブ”工程と、”メイン”工程の2つから成るシンプルな構造です。
サブ工程では、各部品を組み立てておき、最終的なメイン工程で車の組み立てが行われ、完成車が製造されます。
従来は、ひとつの車両に対して順番にサブ工程を挟んでいたものを、事前にサブ工程で並列作業しておくことで、メイン工程の製造時間を短縮できます。
なぜテスラにできて他社にできないのか?
テスラがunboxed processを採用できるのは、部品の内製比率が高いためと言われています。自社部品が多く、社外サプライヤーに頼らないため、工程設計の自由度が高くなり、unboxed processのような劇的な工程変更も素早く行うことができています。
また、車種数が少ないこともメリットで、選択と集中ができていることもテスラの工程の強みになっています。
unboxed processのデメリット
unboxed processには以下のようなデメリットも存在します。
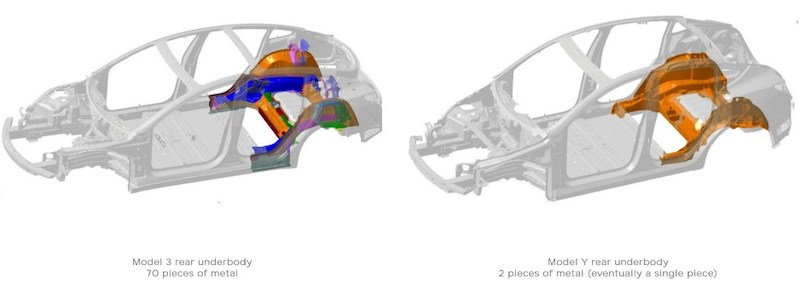
車両をモジュールに分割するため、モジュール間の接合には専用の接合材料が必要となり、逆にコストが高くなる可能性があります。コストを下げるためには、接合部分をなるべく少なくする必要があり、テスラはメガキャストなどの採用によって、部品の一体成型を進めています。
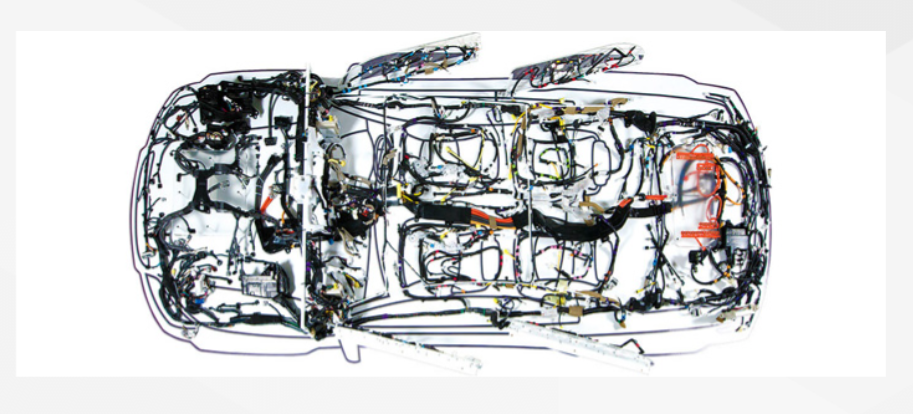
車両全体を這うように設置されるワイヤーハーネスも、モジュール分割するコンセプトのunboxed processでは邪魔になるため、なんらかの対策が必要です。テスラは既にワイヤーハーネスに関する特許を出願しており、ワイヤーハーネスも分割式とすることで、人的設置工数も削減するとしています。
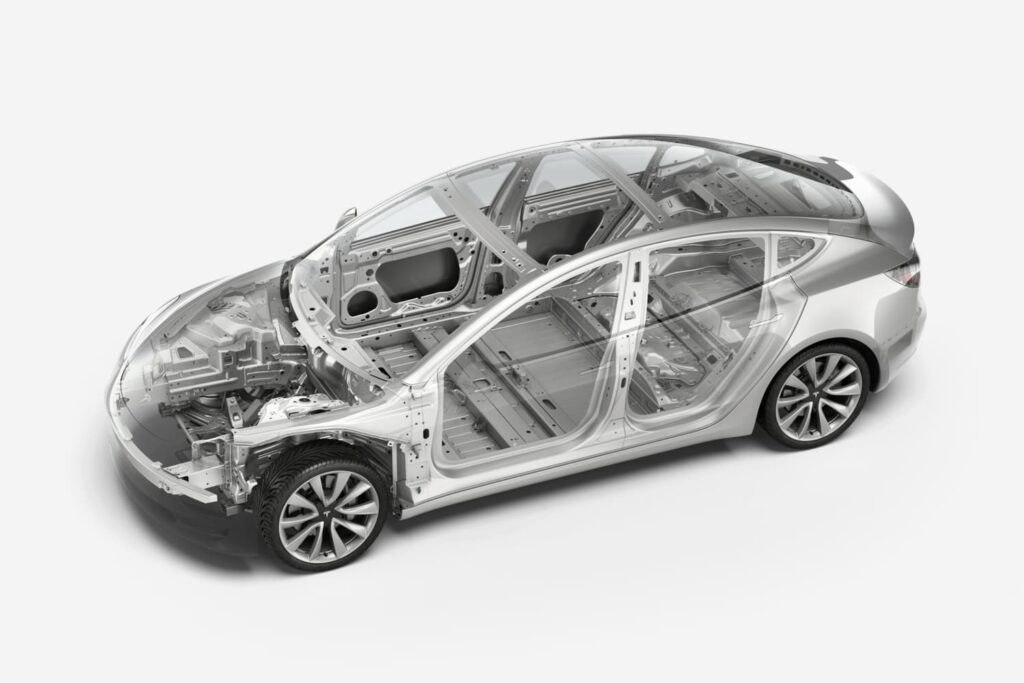
unboxed processのような製造方法は、乗り心地や性能に影響を与える可能性があります。
従来の自動車は、品質や性能、乗り心地を高めるために、部品どうしをうまく擦り合わせて造り込む製造方法です。モジュール間の接合の良しあしによって、車の剛性や遮音性、防振性能などが高い品質を維持できるのかが変わります。
品質を担保したまま低コストを実現できるのかも、注目すべきポイントです。
狙いはテスラの次世代EV
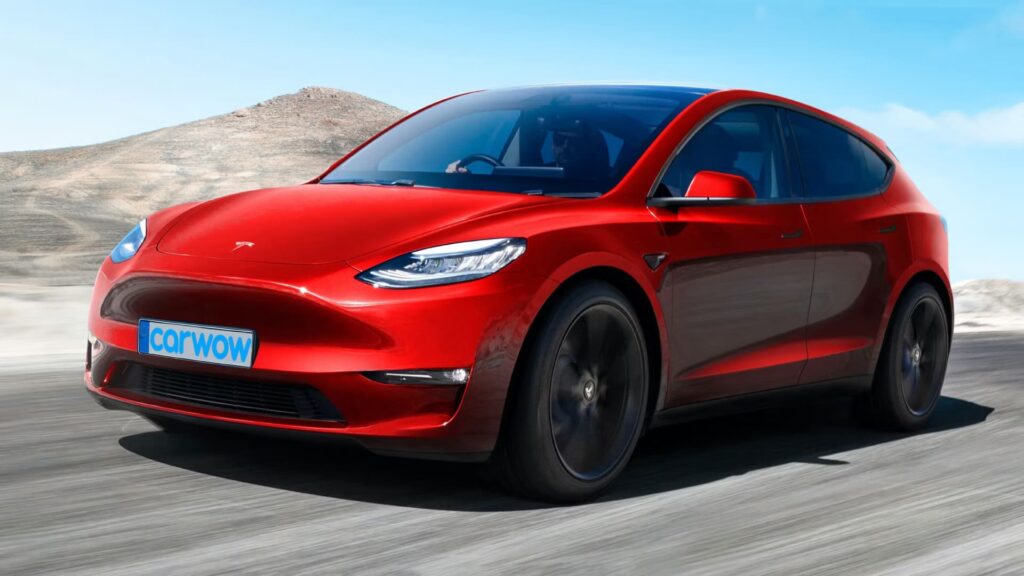
テスラのunboxed processは、価格2万5000米ドル(375万円)ともされるエントリーグレードの車両、モデル2(レッドウッド)を実現するために、車両コストの低減を実現する一つの技術として開発されています。モデル2は2025年前半にも発表されるのではないかと噂されている車両です。
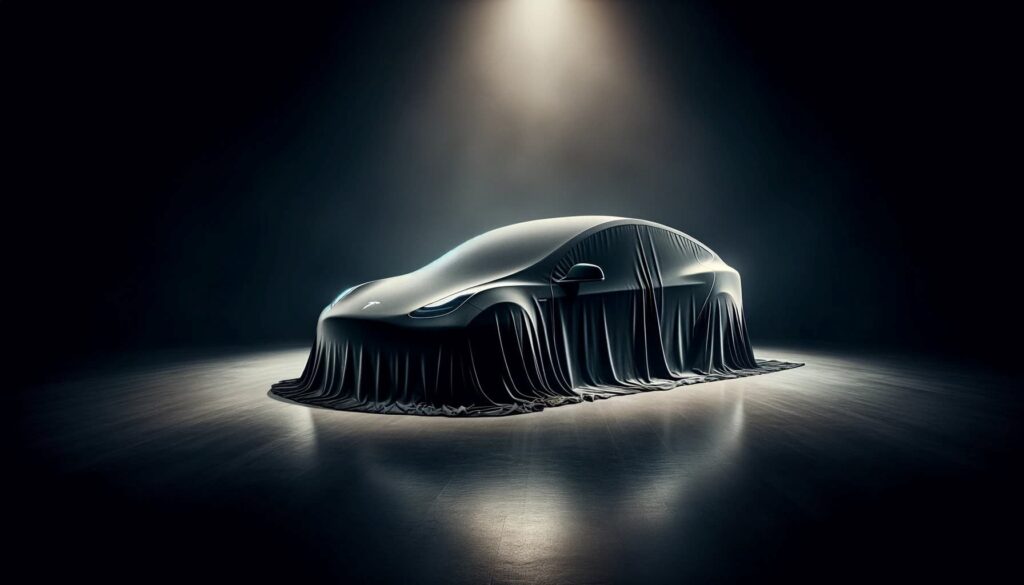
テスラは2024年からUnboxed Processを採用するとしており、この方式が確立されれば、今後更にコスト競争力の高いEVが投入されていく可能性があります。
テスラの目標は、既存のEVの原価を半減することです。Unboxed Processによって、組み立て工程のコストや工程は5割減らせると考えられます。一方で、部品や材料の費用を50%削減することは困難と考えられ、電池の低コスト化や、開発費の低減、販管費の低減など、テスラの目標に達するには課題が多い状態です。
テスラは何故unboxed processをアピールするのか?
テスラがunboxed processをアピールする背景には、中国勢への危機感が見え隠れします。2022年には世界のEVシェアで中国BYDに大きく迫られています。BYDは出自が電池企業であり、EVのコストの1/3を占める電池を安価に製造できる強みがあります。低コスト車両で攻勢をかけるBYDに対して、テスラも電池以外の部分でコストを削る必要があるのです。
また、革新的な技術力のアピールも継続し「先進的な企業だ」というイメージも維持したいのでしょう。自動運転やコネクテッド技術で先進性をアピールしてきましたが、テスラの自動運転(FSD)は結局のところ、レベル2+程度ということはある程度知られているところであり、テスラには技術的な有意差を見出すことが難しくなってきています。unboxed processを実現し、テスラの先進性を世に示したいことも見えてきます。
トヨタも「パクる」ほどの技術
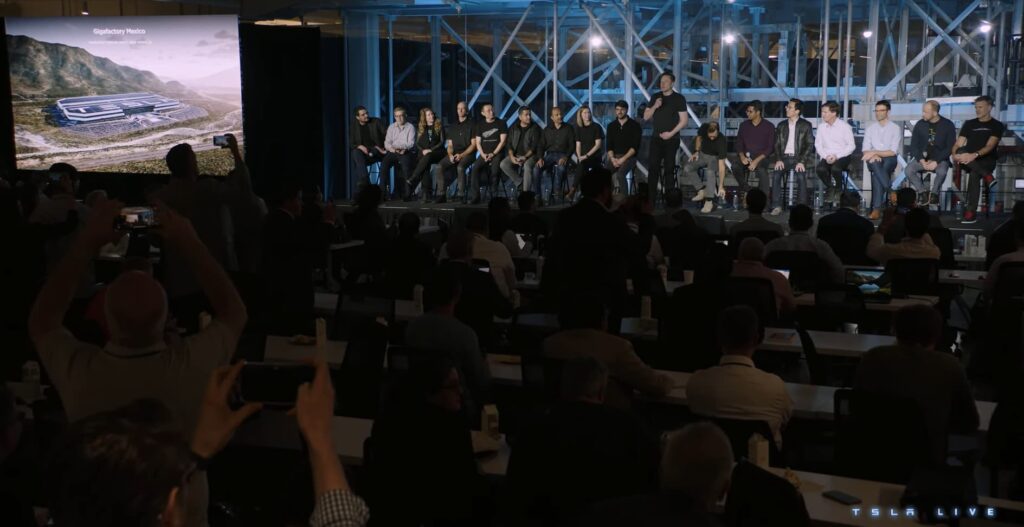
テスラのunboxed processは、自動車製造業界においても大きく注目されています。
ヘンリーフォードが発明した自動車製造ラインが、現代の自動車市場では時代遅れのものであると、各社は気付き始めているのです。
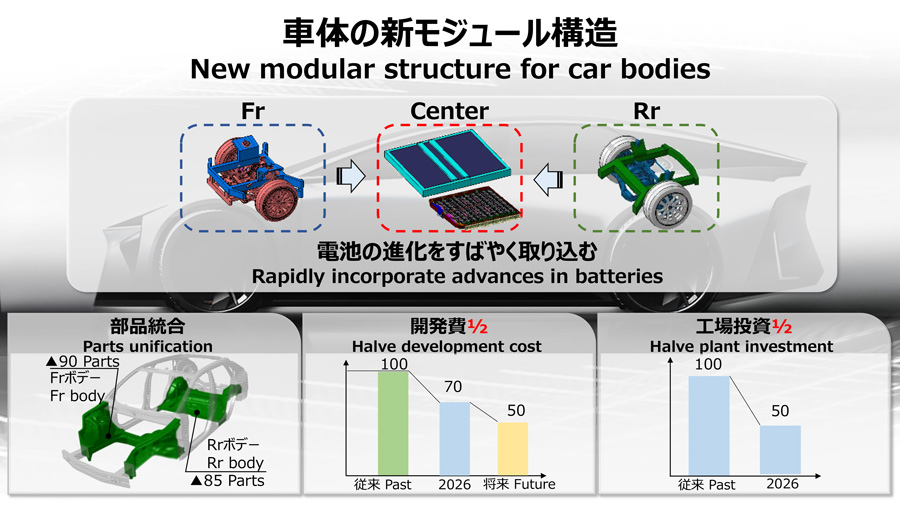
トヨタ自動車は、テスラのUnboxed Processと同じ思想の「車体の新モジュール構造」を提案しています。この目標はテスラとほぼ同じで、開発費と工場投資を1/2とすることを掲げています。
トヨタは2026年のEVからこの工程を実現しているとしており、テスラから2年遅れで巻き返しを図っています。トヨタですらテスラの手法を学び、工程の進化を進めているようです。
まとめ
テスラのunboxed processは、従来の自動車製造とは異なるアプローチです。モジュール化と同時並行の組み上げにより、効率的な生産が可能となります。メリットは工程の削減とコストの削減です。
工程の変化により、乗り心地が悪化する懸念もあります。テスラはUnboxed Processを次世代の低価格EVで実現することを目指しており、2024年から工場での導入を始めます。
テスラの製造方法は革新的な取り組みとして注目され、トヨタなど既存の自動車メーカーも取り入れ始めている重要な技術です。
関連記事
コメント