ゼネラルモーターズ(GM)が開発した「Ultium(アルティウム)バッテリー」が、電気自動車(EV)の新しい潮流を切り開くことになるかもしれません。2024年に北米での発売が予定されている、アキュラブランドの新型EV「ZDX」に採用されるとのことです。
このUltium(アルティウム)バッテリーは何が凄いのか、GMはこの技術を継続的に活用する意思があるのか、解説します。
Ultiumバッテリーは何が凄いのか
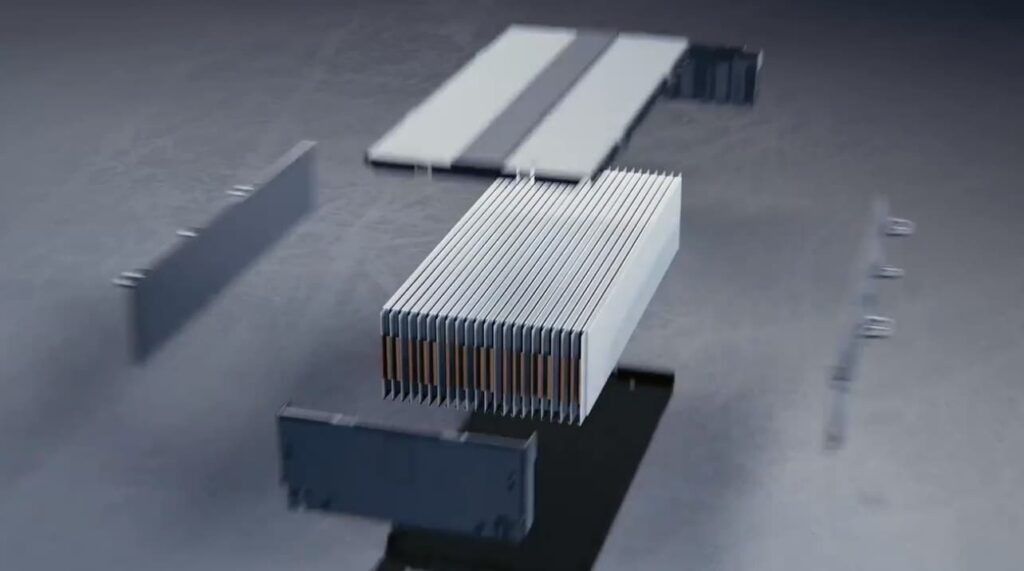
Ultium(アルティウム)バッテリーの大きな特徴は、長いパウチセルを積み重ねるモジュラー設計にあります。
- パウチセルで効率的に配置が可能
- モジュール設計により容量違いのバリエーション化が容易
このパウチセルは、従来の円筒形バッテリーセルとは異なり、非常に効率的に積み重ねることが可能です。狭い空間により多くの電池を搭載できるため、電池以外の要素の設計自由度が向上します。
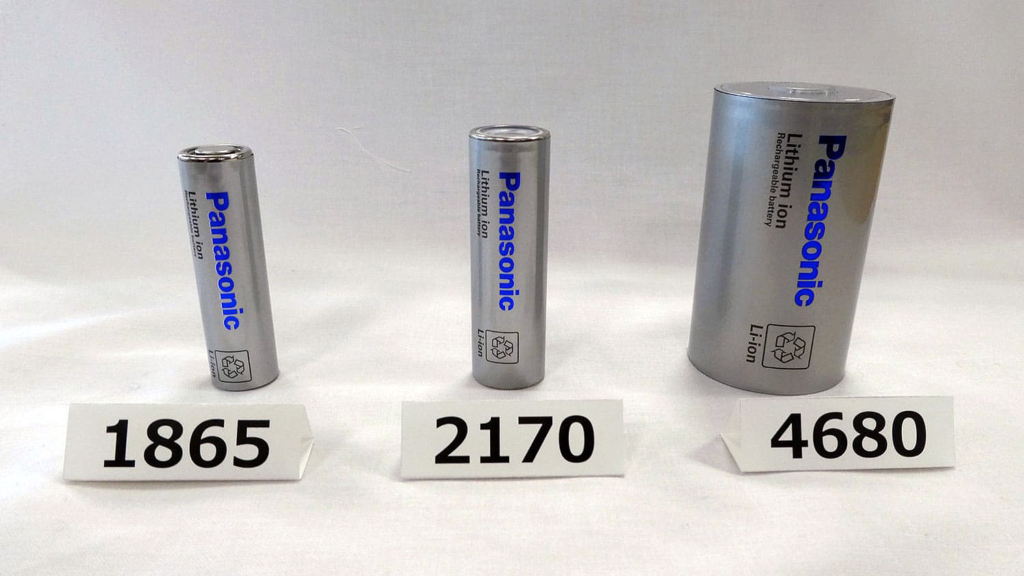
これまで、テスラは円筒形の電池セルを使用していました(1865や2170)。2020年のバッテリーデーでテスラが新しく発表した4680セルも円筒です。
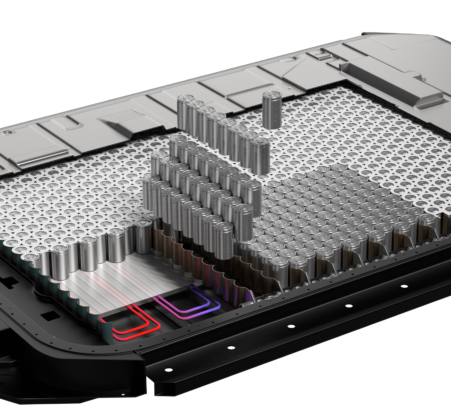
円筒形の電池セルをグリッド状に配置し、それを冷却フィンで冷やす設計がテスラのバッテリーです。
新型の4680のセルでも、冷却方法は変化があるものの、円筒をグリッド上に配置する思想は変わっていません。
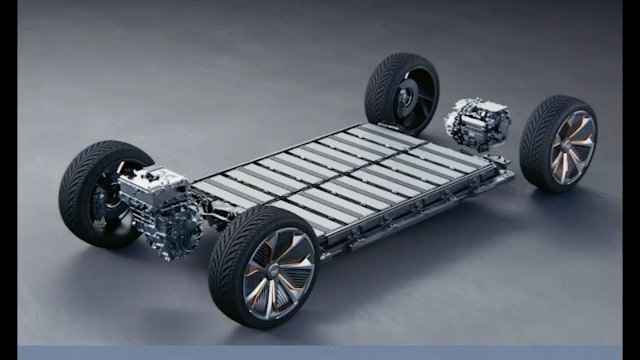
GMのUltium(アルティウム)バッテリーは、パウチ型のセルをグループ化してモジュールを形成し、これらのモジュールを組み合わせて一つのバッテリーパックを形成します。パウチ型セルは、韓国のLGエナジーソリューション (LGES)と設立した合弁会社Ultium Cellsが供給しています。
車両設計の自由度も高い
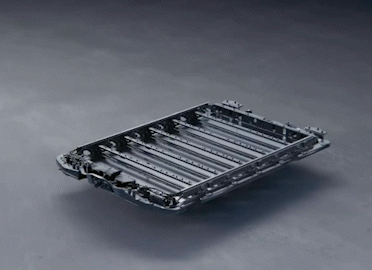
GMのUltium(アルティウム)バッテリーは、電池容量をモジュール単位で設計できるため、同一モジュールを使った複数車種展開が容易です。
モジュールごとに設計することで、各モジュールごとに制御が可能で、電池パックに不具合が発生した際、どのモジュールが不具合を起こしたのか、問題を切り分けることが容易になります。
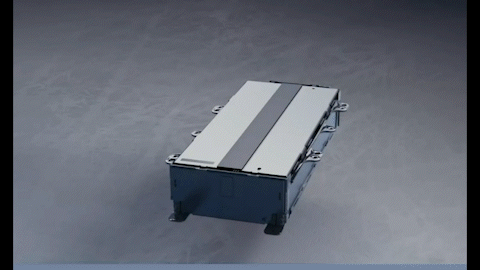
Ultium(アルティウム)バッテリーは50kWhから200kWh以上の範囲で展開され、1回のフル充電で480km以上の航続距離が期待されています。モジュールの数は6、8、10、12、最大24まで変えることができ、車両の種類や要件に応じてカスタマイズが可能です。
モジュール化することで、近年課題となっているバッテリーのリサイクル性も向上します。
GMはパウチ型から切り替えたい?
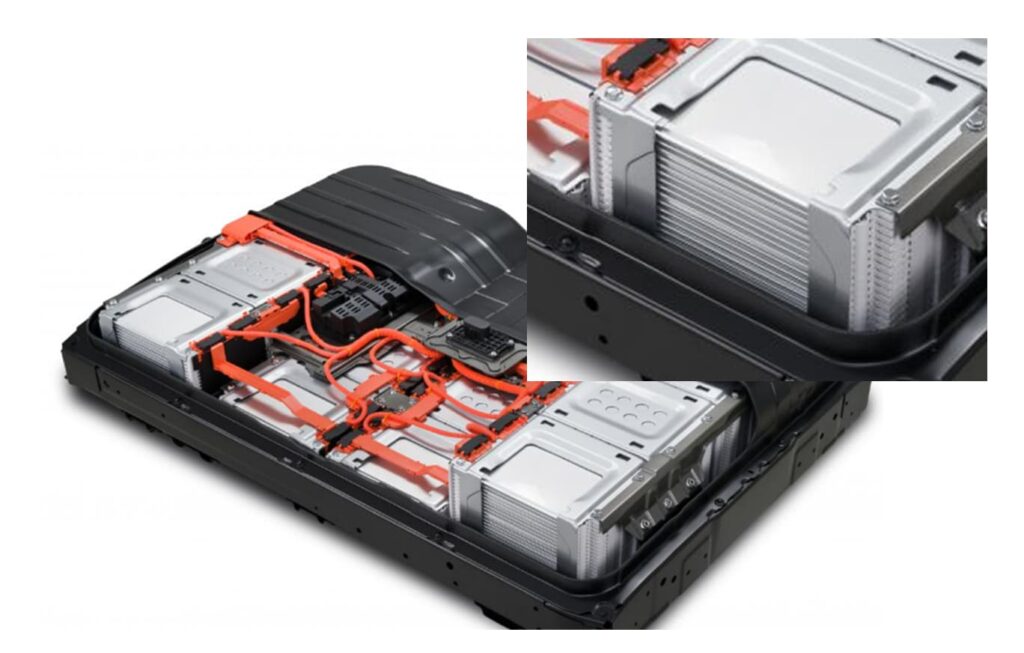
パウチ型セルは、日産のEV「リーフ」にも採用されているセル形状です。パウチ型電池は通常、薄い長方形の形状で、柔軟な外装材で覆われています。軽量なのが特徴で、金属製のケーシングを使用していないため、円筒や角形と比較して軽量、モジュール化に際してもデッドスペースが少なく、高いエネルギー密度を実現できます。
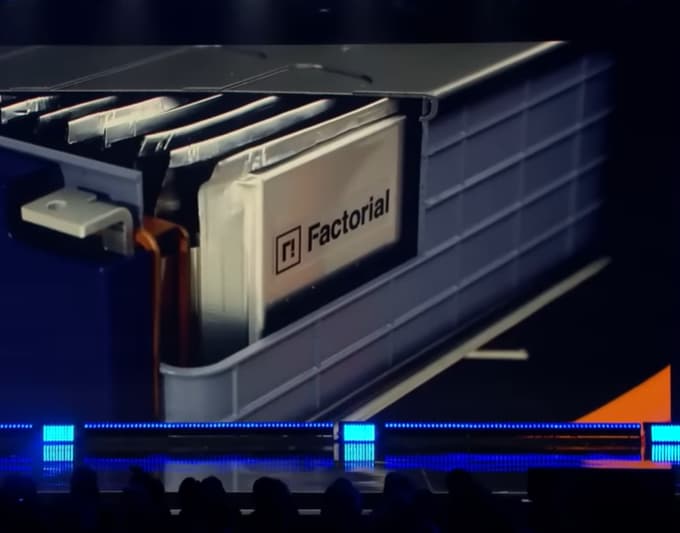
パウチ型セルを用いた電池は近年増えてきており、StoreDotのシリコン負極を用いたバッテリーや、ファクトリアルの全固体電池はパウチ型を採用しています。GMのパウチセルはLGエナジーソリューション (LGES)とGMの合弁会社が供給しており、GMとLGESの関係は強固なものであると考えられてきました。
ところが近年、GMが韓国のSamsung SDIとも提携し、パウチ型バッテリーから円筒型バッテリーへの切り替えを進めているともされています。GMの現在のパートナーであるLGESが「スタッフと能力の不足」により、合弁会社Ultium Cellsが計画していた第4の電池工場の設立計画が頓挫したという事情が噂されています。
筆者の周囲の車載電池を開発するエンジニアも「LGESのバッテリーは燃えすぎ」と評するほど、自動車業界でLGESの電池の安全性に関する評判は良くありません。GMがSamsungSDIに乗り換えようとする理由は安全性と品質にもあるのではないかと想像します。
メリット | デメリット | |
---|---|---|
![]() パウチ型電池セル | 軽量 空間効率が高い 形状が柔軟 カスタマイズが容易 | 破裂や膨張のリスクがある 保護回路の設計が必要 熱の拡散が不均一 |
![]() 円筒型電池セル | 耐久性が高い 一般的に熱的に安定 量産性が高い | 重量が重い 形状が固定されている 空間効率が低い |
![]() 角形(プリズム型)電池セル | 空間効率が高い 電池パックの設計が容易 | 耐久性が低下 熱的に不安定 |
テスラが採用する円筒型セルは、量産性が高く、冷却構造が設計しやすく、また耐久性が高いというメリットがあります。パウチ型セルのデメリットを克服するために、別形状のセルへの移行も検討しているようです。
思想としては若干古い?
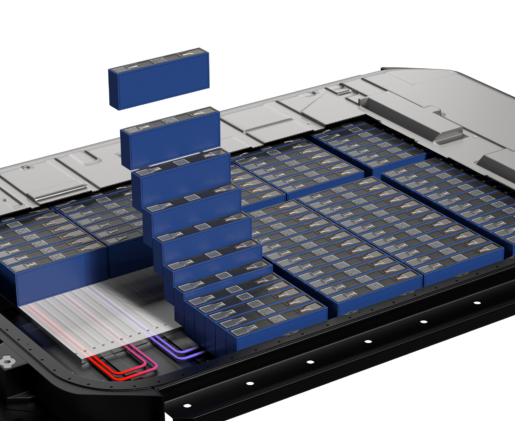
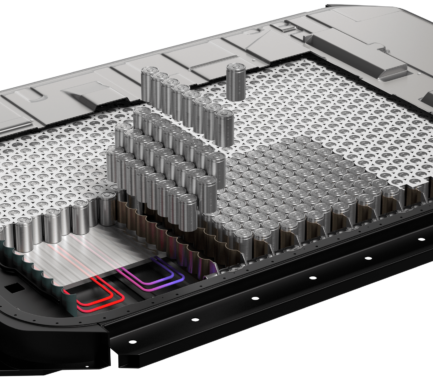
「セル-to-パック(C2P)」や「セル-to-シャシー(C2C)」というアプローチが、EVの車載電池のトレンドとして浮上してきています。
C2PやC2Cは、セルをモジュール化せず、直接パックやシャシーに搭載するというもので、モジュールを排することで狭い空間にバッテリーセルを効率よく配置しようとするものです。
C2Pには、中国CATLの麒麟電池、SVOLTのドラゴンアーマーバッテリーやBYDやトヨタが採用するブレードバッテリーが相当します。
電池セルをモジュール化して車両に搭載するGMのUltiumバッテリーは、C2PやC2Cとは「ひと世代」古い技術と言えます。
かといって、モジュールベースの設計がC2P技術に劣っているかというと、必ずしも「劣ってはいない」と言えます。C2Pにもモジュール設計にも、それぞれにメリット・デメリットが存在するためです。
モジュールベースの設計は、障害が発生した場合の影響を局所化するという安全面でのメリットがあり、リサイクル性にも優れています。
麒麟電池やブレードバッテリーは実用化に至ったばかりで、信頼性の点では懸念材料も多いです。GMとしては、まずは信頼性の高い確立された技術でEVを販売したいという思惑もあるのでしょう。
まとめ
GMのUltium(アルティウム)バッテリーを紹介しました。LGESの提供するパウチ型セルをモジュールに配置し、モジュールの数を制御することで、車種ごとに電池容量を容易に設計可能となる技術です。
GMがこの技術を継続的に活用するかは不透明で、パウチ型から円筒電池に切り替え、Samsung SDIが円筒電池を供給するともされています。また、セルをモジュールに配置する思想は電池搭載の効率が悪く、セルtoパックなどの新技術が採用されていく可能性があります。
今後も動向を注視していきます。
コメント